1988年に登場したソニーの「MDR-R10」は、オーディオを本格的に楽しむことを目的に開発されたモデルで、製造が終了して20年が過ぎた現在でも人気が高い(既に修理対応は終了。中古品の場合は製品の状態が不明のため、本来のパフォーマンスが体験できるかは保証できません)。この製品の開発にあっては、ヘッドホンとしての音のよさはもちろん、装着した際の心地よさも重視し、実に細かい配慮が施されている。中編となる今回は、MDR-R10に盛り込まれた素材や技術、さらにはそれらを採用した “想い” について解説いただく。(StereoSound ONLINE編集部)
ヘッドホン:ソニー MDR-R10 ¥360,000(生産終了。発売当時の価格)
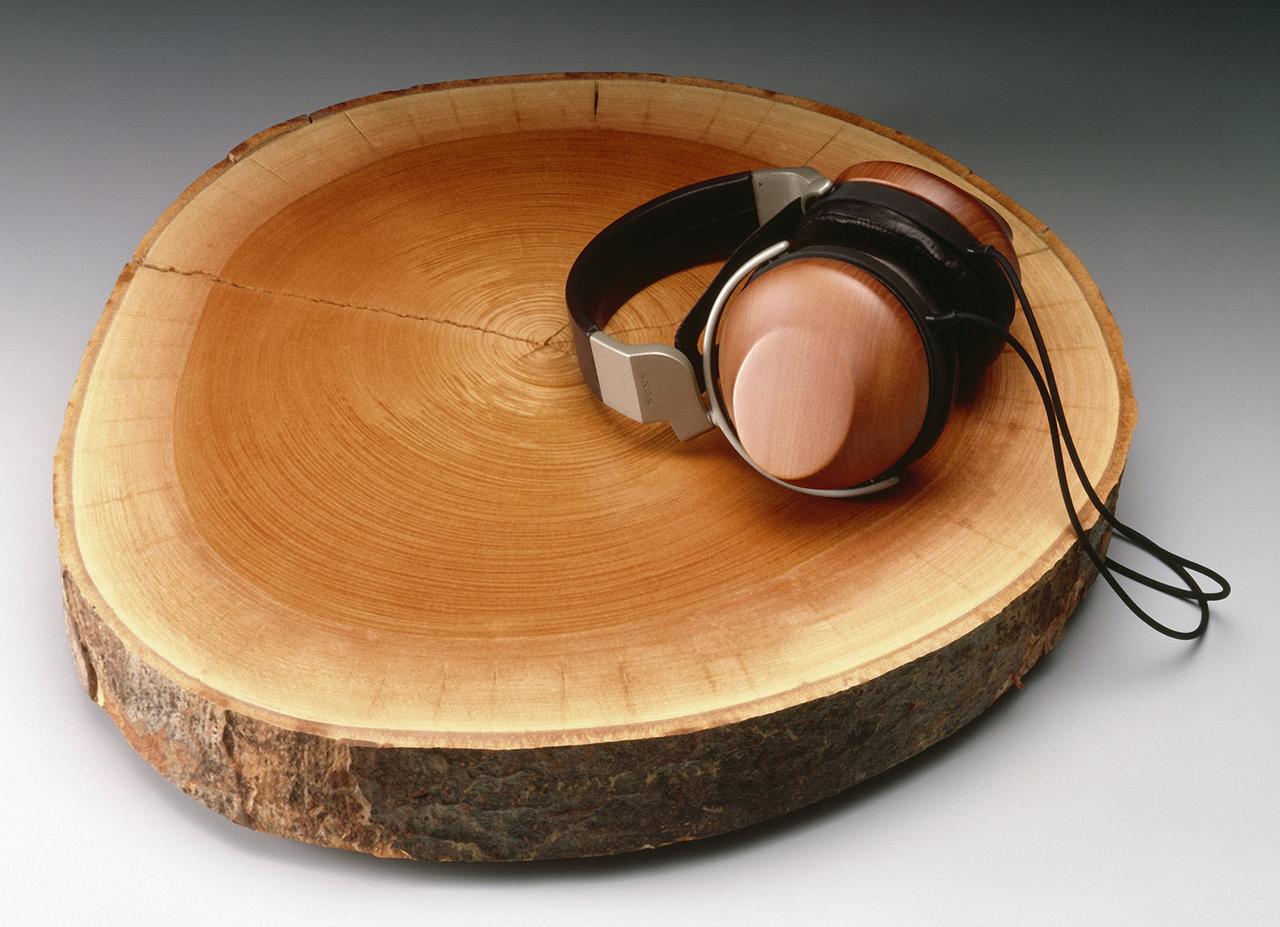
●使用ユニット:50mmドーム型バイオセルロース振動板●インピーダンス:40Ω●音圧感度:100dB/mW(1kHz)●定格入力:300mW●再生周波数:20Hz〜20kHz●質量:400g(コード含まず)
§7 フラッグシップモデルの開発 その2
「10倍の値段で売れる商品を作る」ということで始まったMDR-R10(以下『R10』と略記)の開発ですが、楽器のように木質筐体の響きを活かすことで活路を見出し、さらには機種全体で天然素材の音や機能性、質感のよさを追求する活動に入っていきます。今回は、その中でのいくつかの部品について、その開発経緯や技術とそこに託した思いなどをご紹介させていただきます。
1)バイオセルロースの振動板
当時、ヘッドホン用のドライバー振動板の材料としてはPETなどの高分子フィルムを使うことが一般化していました。しかし、スピーカーのコーンとしては、最高級機種でも紙素材によるものが多く存在していました。ヘッドホンもかつては、紙コーンを流用した小型のダイナミック形ドライバーを搭載した製品が多く存在していました。しかし1980年代以降のヘッドホンでは、より高感度で広帯域の再生を求めて振動板の軽量化、薄膜化が進んでおり、6〜40μm前後の厚さが一般的になってきている中で、100μmほどの太さを持つパルプ繊維を用いた紙コーンは使いにくい状況になっていたのです。
そんな中で、ソニー社内の材料開発部門から新しい材料の紹介があったのですが、それが「バイオセルロース」でした。バイオセルロースとは、アセトバクターというバクテリアが糖から産生する純粋なセルロースの繊維材料です。これはそもそも、味の素株式会社が食品用に開発したものが当時の通産省工業技術院(現経産省産総研)に持ち込まれ、用途開発の可能性検討に上がっていたもので、その応用可能性の打診がソニーにあった、という経緯になります。
セルロースはまさに紙の主成分であり、新機種の目指す音の方向性に合致する期待が持てるとともに、このセルロース繊維は300Å(0.03μm)という極細繊維でしたので、最新のヘッドホン振動板としても充分に使える可能性が高い素材と思えたのです。こうした経緯で3者共同の振動板開発が始まりました。
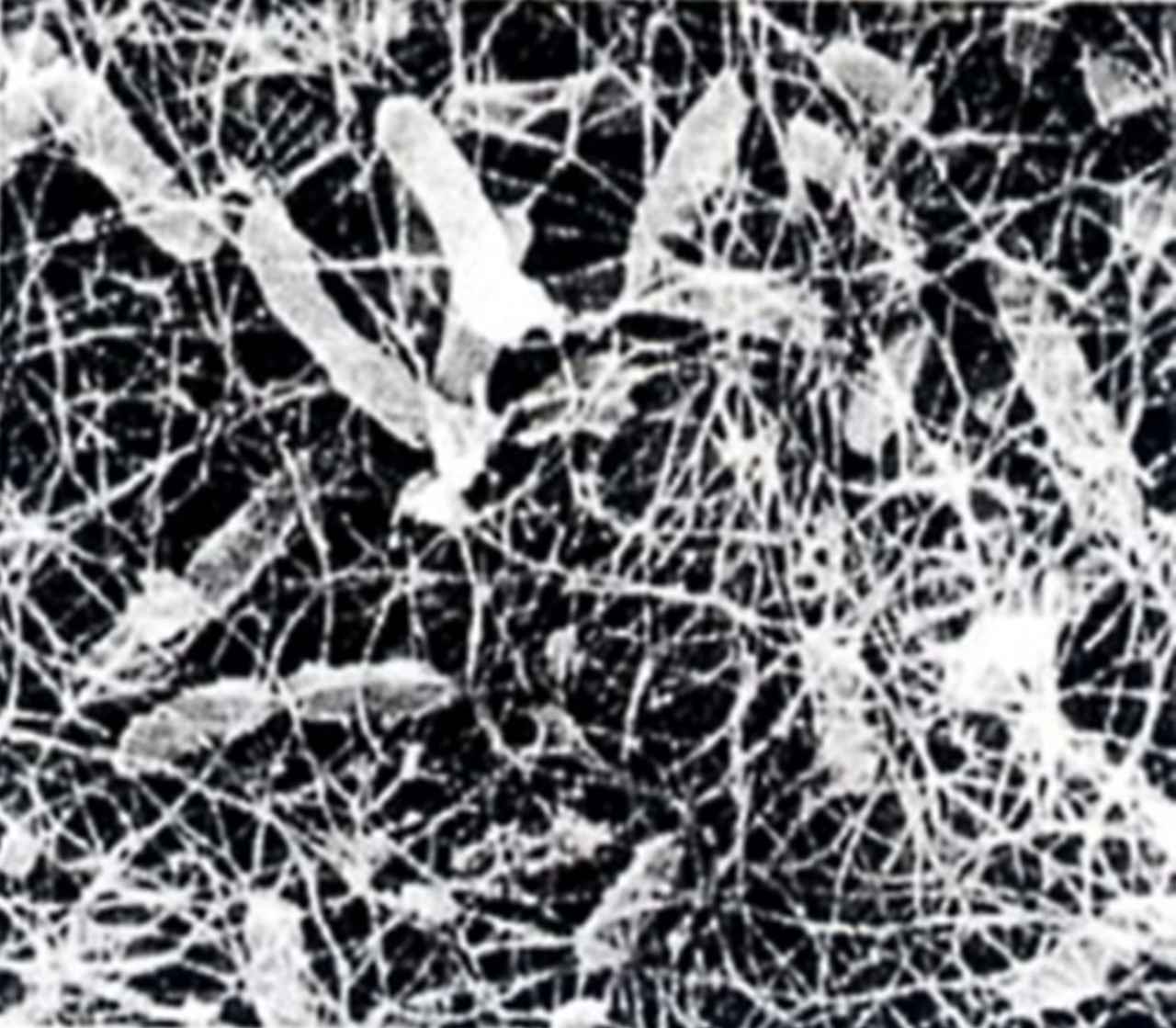
アセトバクターとバイオセルロース繊維
この新材料を使いこなすには、音質的に最適な仕様の検討もさることながら、量産の製法や耐久性の向上のための多くの試行錯誤もあり、最終的には次のような製法でヘッドホンの振動板を実現することができました。 まず、ビーカーに入れた加糖水にアセトバクターの株を浮かべると、空気との界面に巣を張るようにセルロース繊維を産生してゆき、その厚みが4mm程度にまで育ったところでゲルを取り出します。このゲルを、上下の型で加圧脱水しつつ加熱することで、20μmの厚みの振動板が完成するのです。
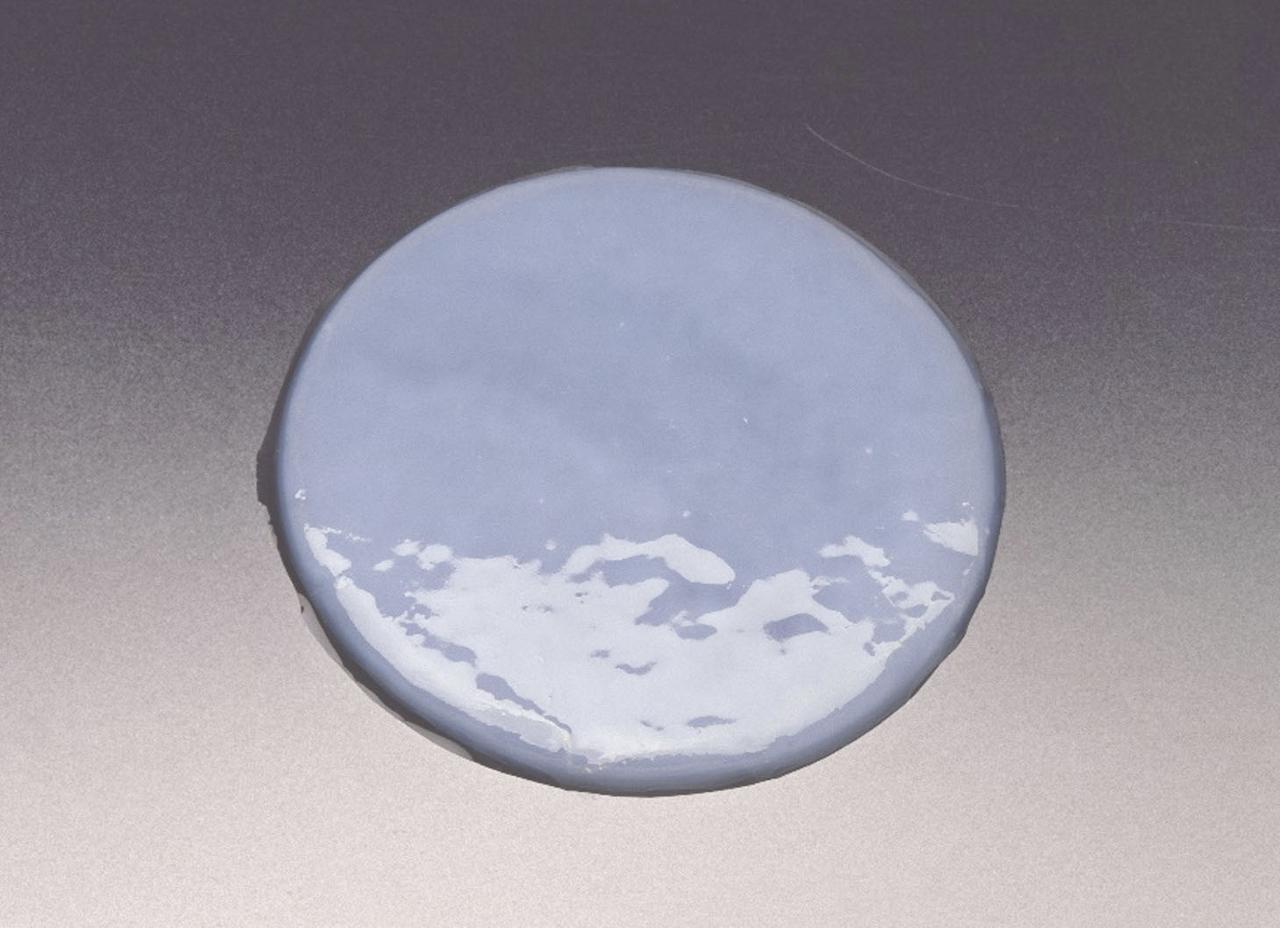
バイオセルロースのゲル
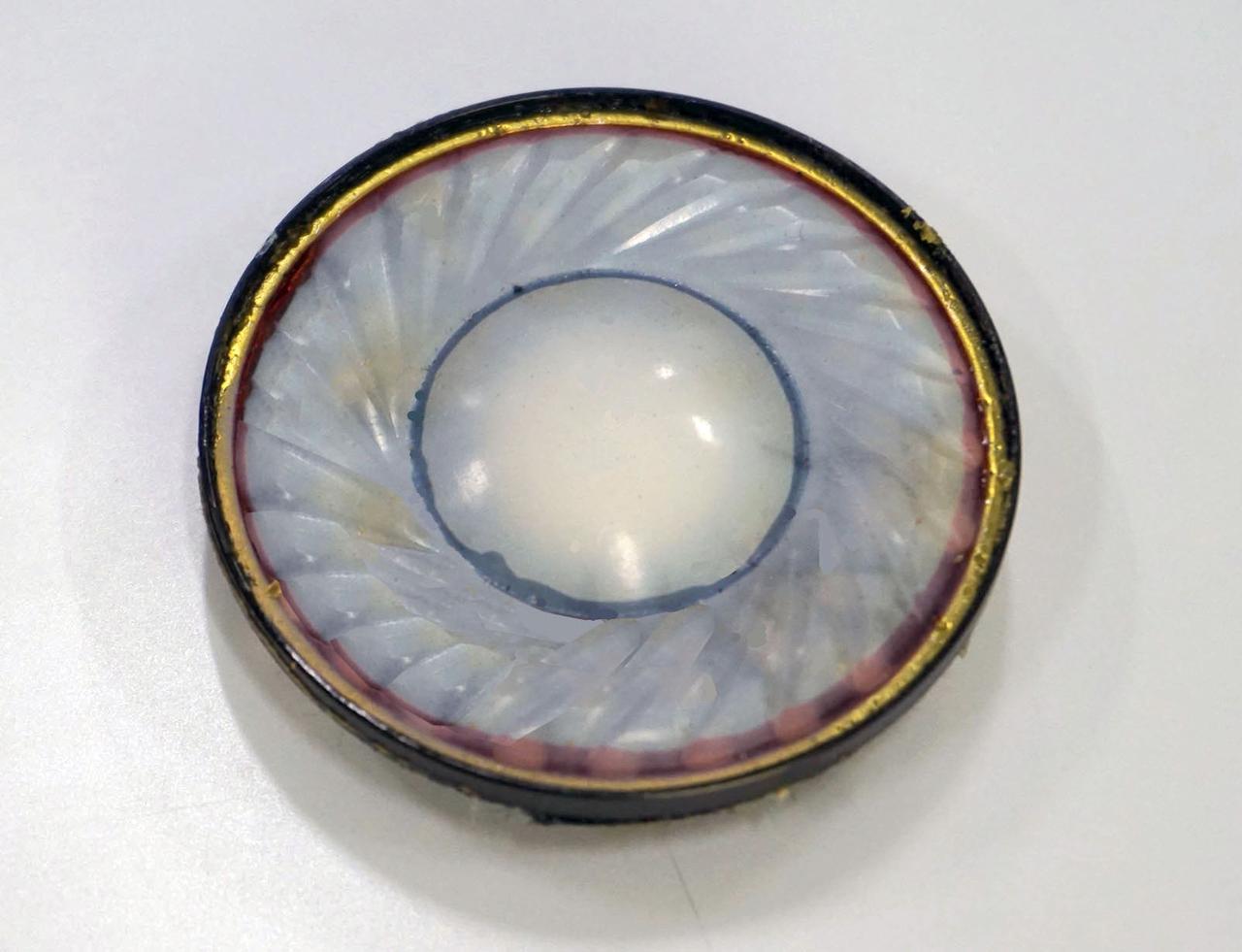
バイオセルロースを使った振動板
こうして実現した、ピュアセルロースによるヘッドホン振動板。試聴結果は従来の高分子フィルム振動板の高感度・高音質を満たしつつ、紙の音の素性と共通する音色を感じられて大変良好なものとなりました。
更に振動板としての物性にも注目してみると、バイオセルロースは驚くべきデータが得られましたので、以下でそれを紹介します。
振動板の素材というものは、一般的な物性としては軽くて硬く、固有音が少ないものが望ましいとされています。軽くて硬いと、駆動コイルの位置から周辺に伝わる波の速度が速いことになり、振動板全体が一体となって振動することで高音まで広帯域に再生できる、重要な要素なのです。また、特定の周波数に材料固有音としての共振が強く出ると、楽音信号として入力した音にその材料の音質が加味されてしまって音質を損なうことがあり、材料としての制振制のパラメーターも重要になってきます。
そのような振動板材料の素性データは、音速の2乗に相当する「比弾性率」と、制振性に関する「内部損失」という、素材の二つのパラメーターのグラフで振動板の素材の物性を評価することができます。このグラフの見方としては、二つのパラメーターがより高いレベルで両立している方が望ましいので、右上の方向に進化軸があることになります。
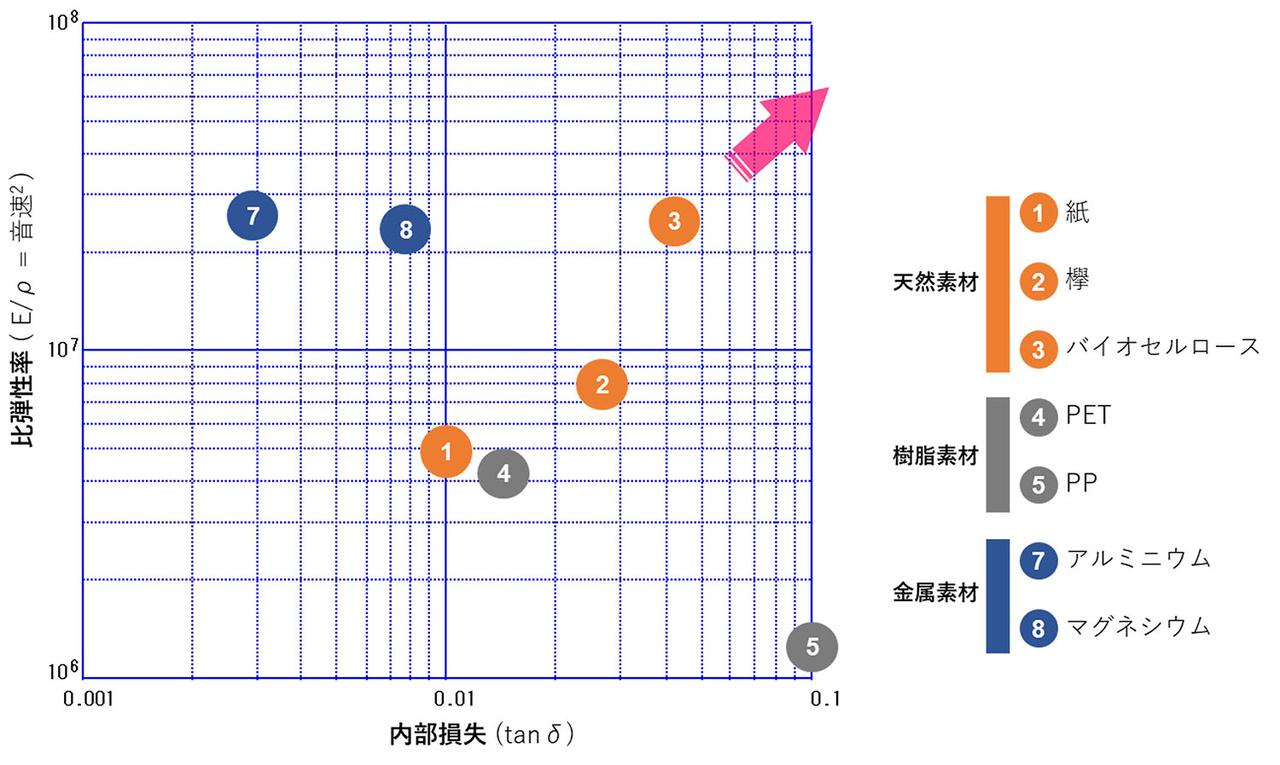
例えば、金属材料は比弾性率が高いものの内部損失が低いので、高音の再生に向きますが金属の固有音が付帯しやすい傾向にあります。柔らかい樹脂であるポリプロピレンは内部損失が高いものの比弾性率は低いので、高音域までカバーする振動板には不向きです。そんな中で紙やPETは二つのパラメーターをバランスよく有していて振動板としては優等生なのですが、さらにバイオセルロースは金属並みの比弾性率を持ちながら高い内部損失も実現するという優れた特徴があることが分かりました。
こうして、R10で目指す音質再現に向けて筐体材料と振動板材料の開発を大きく進めることができたのです。
2)ラムスキンのイヤーパッド
ヘッドホンの音質はもちろん重要ですが、私は装着性も音質と同等に重要な要素だと思っています。ヘッドホンは人が装着する唯一のオーディオ機器なので、洋服の着心地や靴の履き心地と同じで、フィット感が悪いと身に着けたくなくなりますし、音楽を楽しむ気持ちにはなれないとさえ感じます。そこで、次に取り組んだのはイヤーパッドの開発でした。
R10では、木質筐体の響きを最大限に引き出す目的で120mmというヘッドホンとしては最大径の筐体を目指しましたが、これは装着可能なイヤーパッドの最大径としてこのサイズが限界だったからです。120mmの大きな外形で頭部への接触面積を最大化し、接触部分の圧力を分散させることで快適な装着性の追求を行いました。
まず検討したのは、クッション素材の柔軟性でした。一般的に、ヘッドホンのクッション材に使うウレタンフォームは硬度でいうと100N(ニュートン)という硬さで現わされるのですが、当時入手可能な中でもっとも柔軟な硬度4Nのフォームを上層に、硬度14Nのフォームを下層にと、2枚を異形状で重ねて、限界までの柔軟性を持たせつつ、頭部の立体形状に沿う曲面のベースを作りました。形状的には、内径は耳介の外形に沿った形にしつつ、耳の下後方部に厚みを持たせ、耳介の立ち上がりを圧迫せずに、完骨と呼ばれる頭部のくぼみにフィットするように工夫しました。
次の問題は皮革の処理でした。一般的にぬいぐるみのような造形物は中のクッションがある程度硬く、その上に皮を引っ張って伸ばすことで立体的な形を作っていきます。しかし、今回のイヤーパッドクッションでは極端に柔軟なクッションを採用したため、皮を伸ばそうとするとクッションがつぶれてしまって厚みや立体形状が出てこないことになります。そこで、皮革のスキン縫製は、皮革を表、裏、内、外の4枚に分け、これらを立体縫製することによってクッションのつぶれを最小化することで柔軟性を出すことにしたのです。
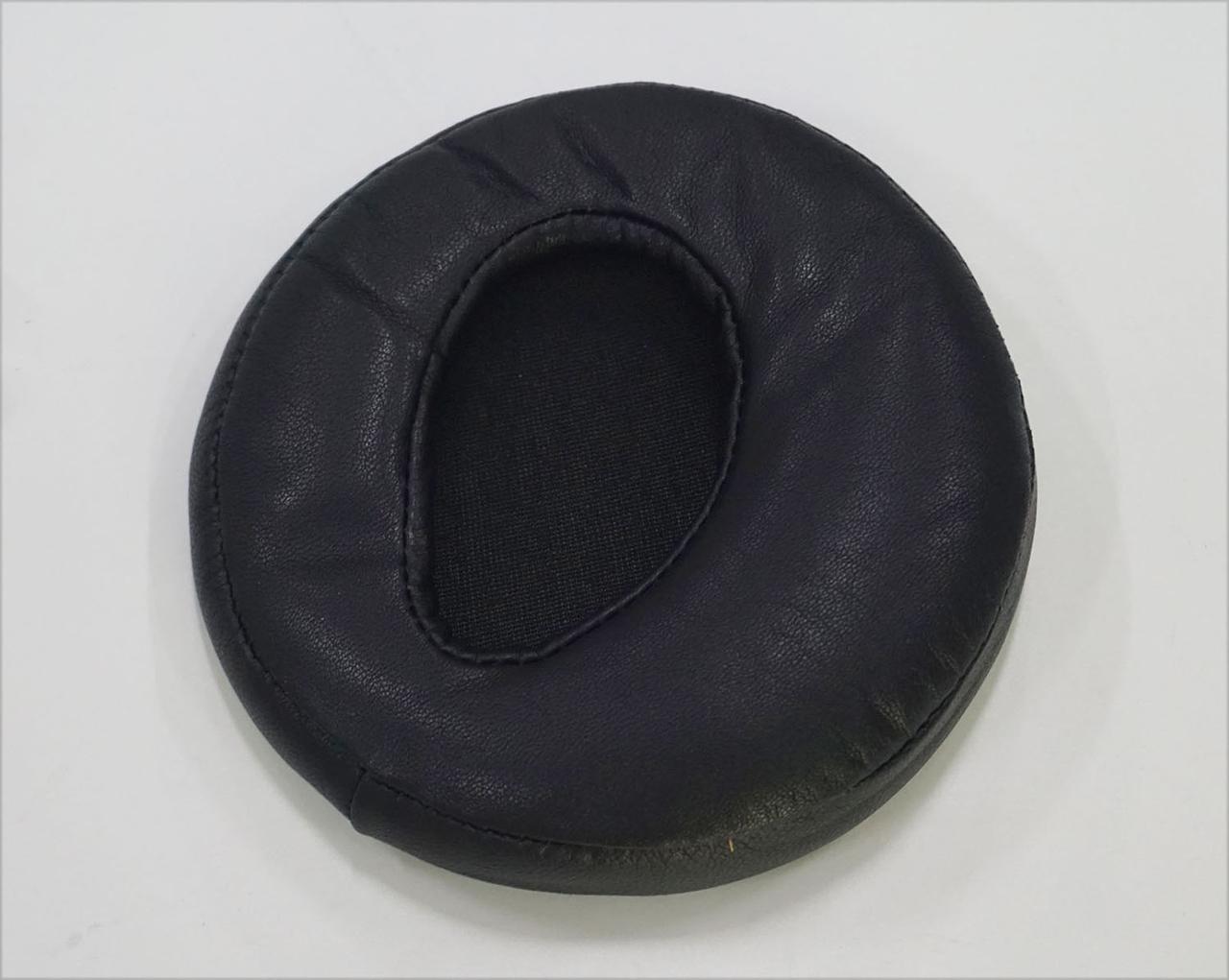
R10のイヤーパッド
R10のイヤーパッドの皮革素材としては、ビニールなどの人工的な質感でなく人肌になじみやすい天然皮革に挑戦することは決めていましたので、最終的に天然皮革の選定に取り組みました。
ひとくちに皮革材料といっても牛革や豚革など色々ありますが、今回のクッションを包む皮革材料としては圧倒的に柔軟性と伸縮性が必要になるのです。そこで、皮革卸商を訪ねてお勧めいただいた中でもっとも柔軟性の高い食用ラムのスキン(子羊の皮)を有効利用することにし、0.5mmという限界の厚みで漉いてもらい、これを縫い合わせる仕様にしました。
この特製の皮は柔軟性がひじょうに優れており、肌触り、手触りがとてもよかったので、イヤーパッドだけでなくヘッドバンドやサスペンダーと呼ばれる柔軟性の必要な機能部品の全てを包むことにしました。このため、ヘッドホン1台製作するのに要する皮の面積はほぼ子羊1頭分に相当していますが、このように贅を尽くした仕様ならではの装着性を実現できたのではないかと思っています。
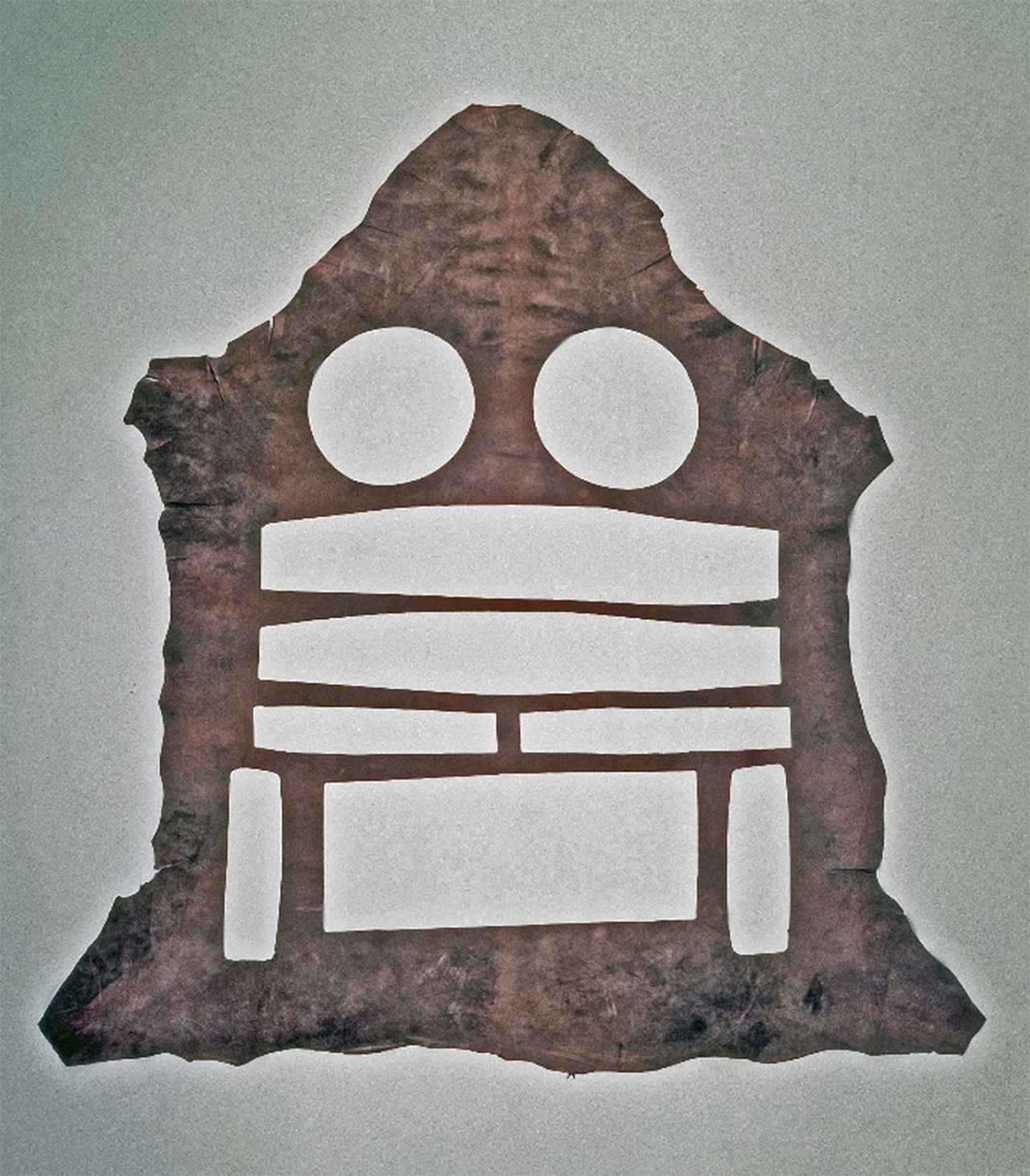
ラムスキンの使用面積のイメージ
余談ですが、この立体縫製は縫製技術の難易度が高く、イヤーパッドのメーカーでもベテランの職人一人しか作れなかったため、その方が出社できない時には部品の生産が止まることもあったことも思い出されます。
3)シルク編みのコード
ヘッドホンの入力コードの導体の材質としては、最高の評価を得ていた6N(99.9999%の純度)のLC-OFCを同軸撚りで使用しました。また、プラグの材質にはOFCを使用し、耐摩耗性が高く導電性のいいロジウムメッキの上に、耐腐食性が高く接触抵抗の低い純金メッキを施しました。過去の検討の中で導体材料として最高だったものから、従来機種では採用できなかった構造を実現したのです。
更に検討を進めたのは、ヘッドホンコードとしての手触りと絡みにくく弾力がある被覆構造でした。ここではまず、コードを束にしたり、折り畳んだりしても癖がつかない復元性の良いシリコンゴムの中間被覆を用いました。
その上で、最終の仕上げとしてシルク糸を編み上げることにトライしました。編み紐コードは後に製品化されたファッション系ヘッドホンなどでもブームにもなった製法ですが、R10での試作当初は、社内でも「こたつやアイロンの電源コード」と揶揄されるくらい散々な出来だったのです。しかし、従来のビニールコードから大幅な手触りの向上もありますし、表面の滑り易さによって絡みにくくなるという観点から、シルク編組の被覆のコードが最高という信念をもって試作を進めました。
最終的にシルクの編み目を可能な限り細かくすることで滑らかな表面になり、理想的な手触りのコードが実現できたと思います。表面のスムーズさを出すために、編組の機械として神奈川県の工業試験場にしかなかった30打ち(編み込み機械で糸の持ち手の数が30本)という仕様を採用したのですが、編組の限界仕様を見極めることができました。
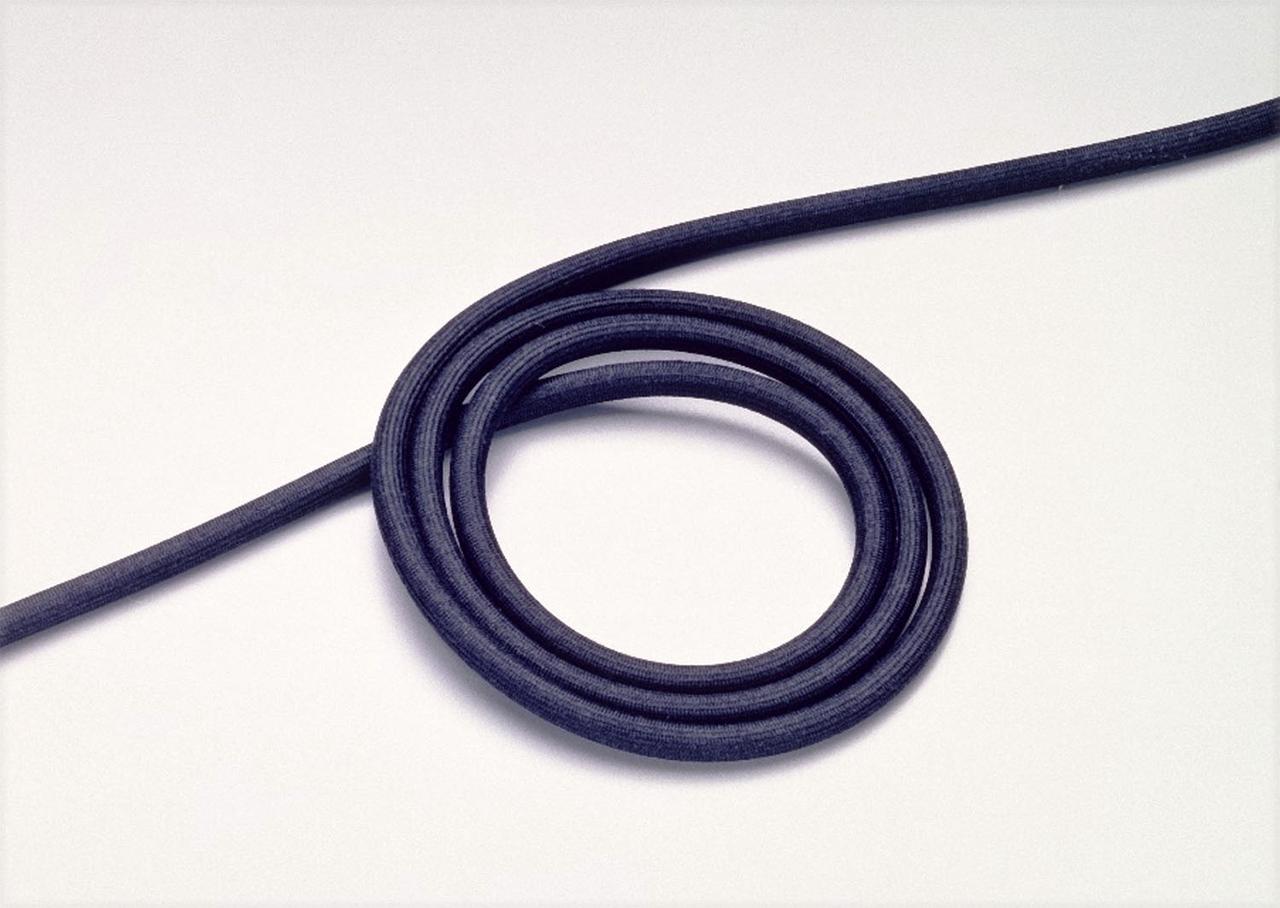
シルク編みのコード
4)最先端材料による装着機構
天然素材を多く採用したR10ですが、実は機構部品には当時の最先端素材も多く使用していますので少し紹介します。
ヘッドバンドは、ヘッドホンを保持するだけでなく、側圧を与えるという重要な役目も果たします。この側圧は、ハウジングと耳の間に適度な音響空間を作る上で必要不可欠な圧力です。
一般的なヘッドホンでは、ヘッドバンドにステンレス材を使用しています。しかし、R10では、ひじょうに軽く、かつ充分な側圧が得られるカーボンファイバーコンポジット材を採用しました。比重は、ステンレス7.8に対し、カーボンファイバーは1.62と、より軽量。比弾性率は、ステンレス2.5に対し、カーボンファイバーは9と、より強くしなやかです。さらには、ステンレスより振動減衰性に優れているため、不要な共振を抑え込みます。
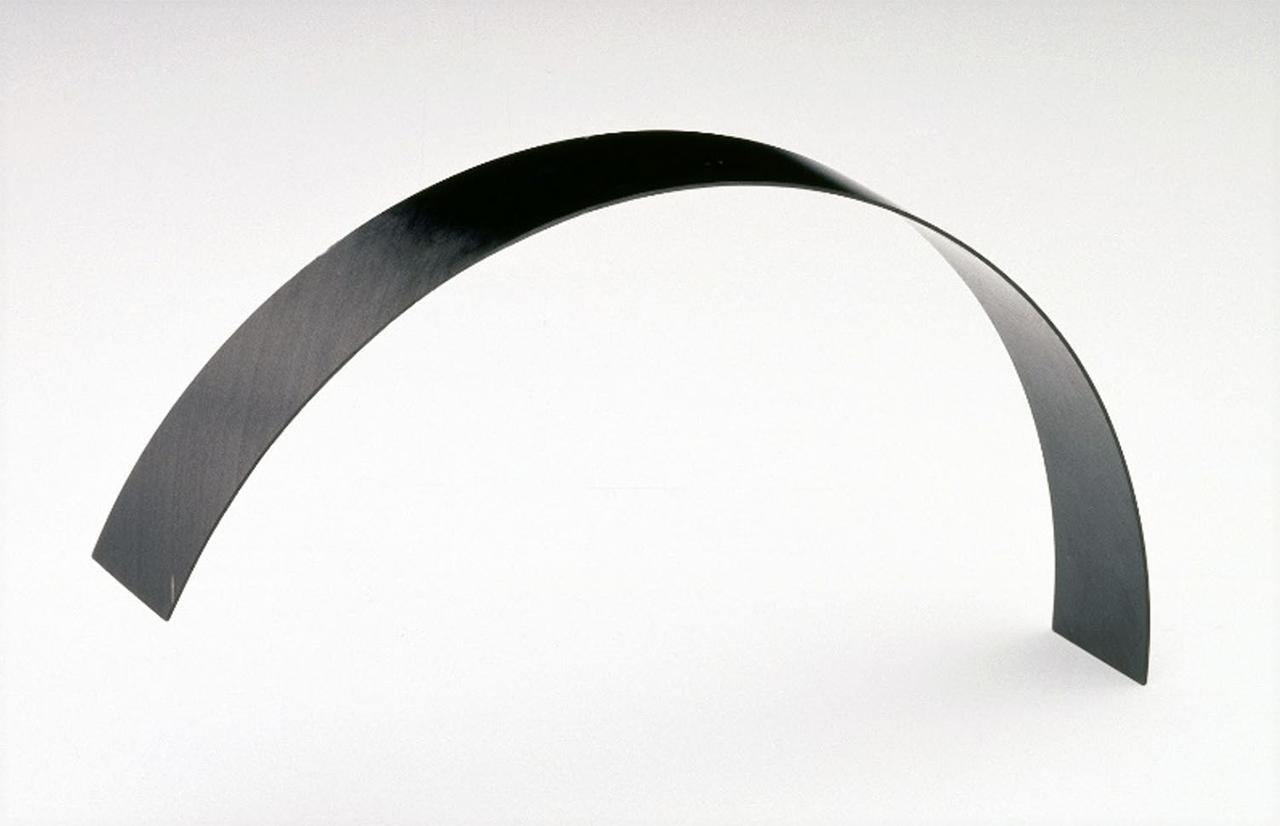
カーボンファイバーのヘッドバンド
それまでの多くのヘッドホンでは、装着する場合に位置を手で調整する方式を採用していました。しかしR10では、頭にセットし、ハウジング部を耳の高さにもっていくだけで自動的にハウジングの位置が決まるフリーアジャスト方式の構造を搭載。そのために、サスペンダーの張力を与えるスプリング材としてチタン・ニッケル系の形状記憶合金を採用しました。
これは、形状記憶合金の持つ「超弾性」と呼ばれる特徴を利用したものです。形状記憶合金の変位(タワミ)が、あるレベル(超弾性領域)まで達すると、荷重はそれほど変化しなくなります。しかも、弾性領域を超えると元にもどらなくなるステンレスなどと違い、形状記憶合金は元の形にもどります。つまり、形状記憶合金を採用したヘッドバンドは、誰が装着してもほぼ同じようにジャストフィットし、長期間使用しても伸びきらないということになるのです。
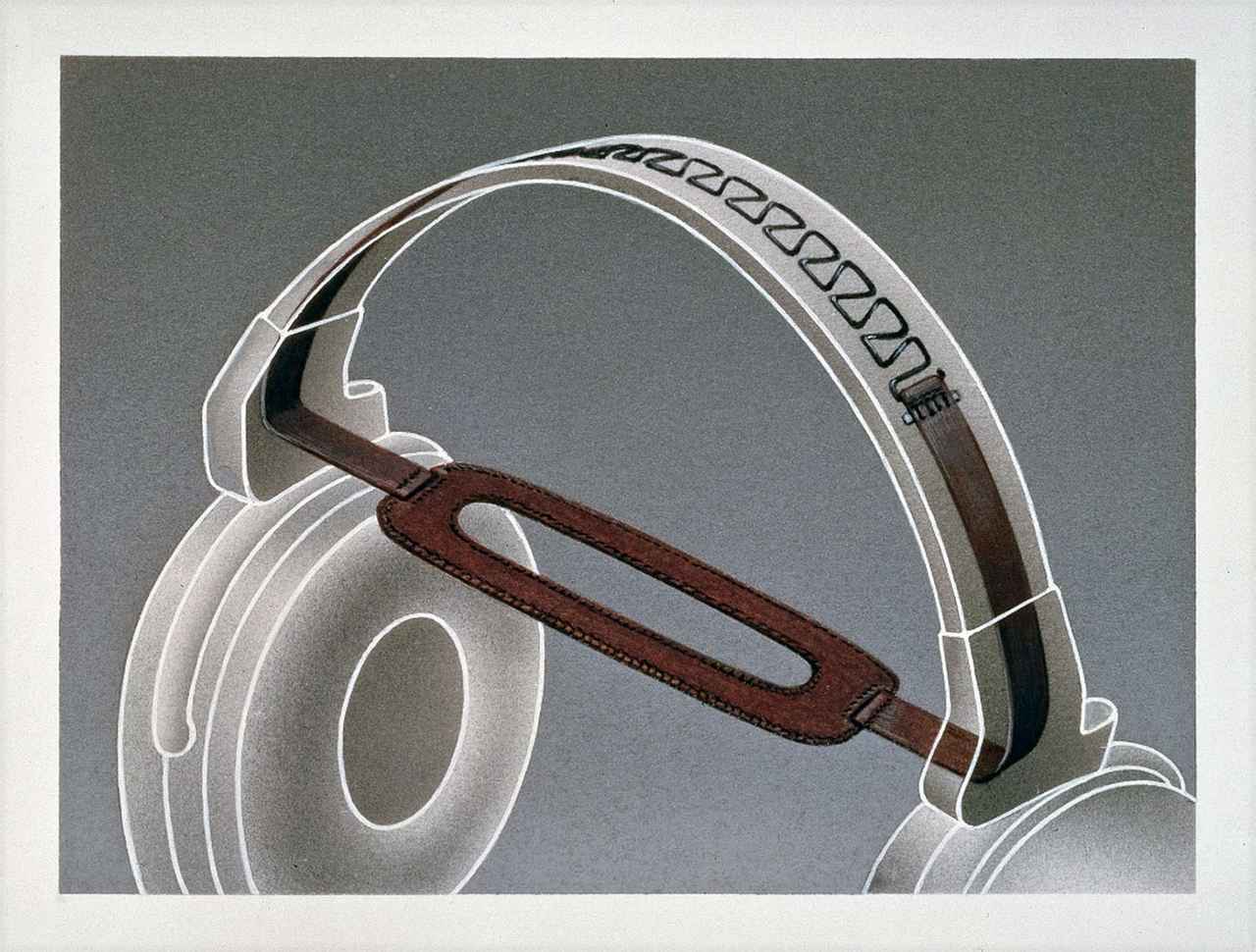
形状記憶合金を使用したヘッドバンドの長さ調整機構(透視図)
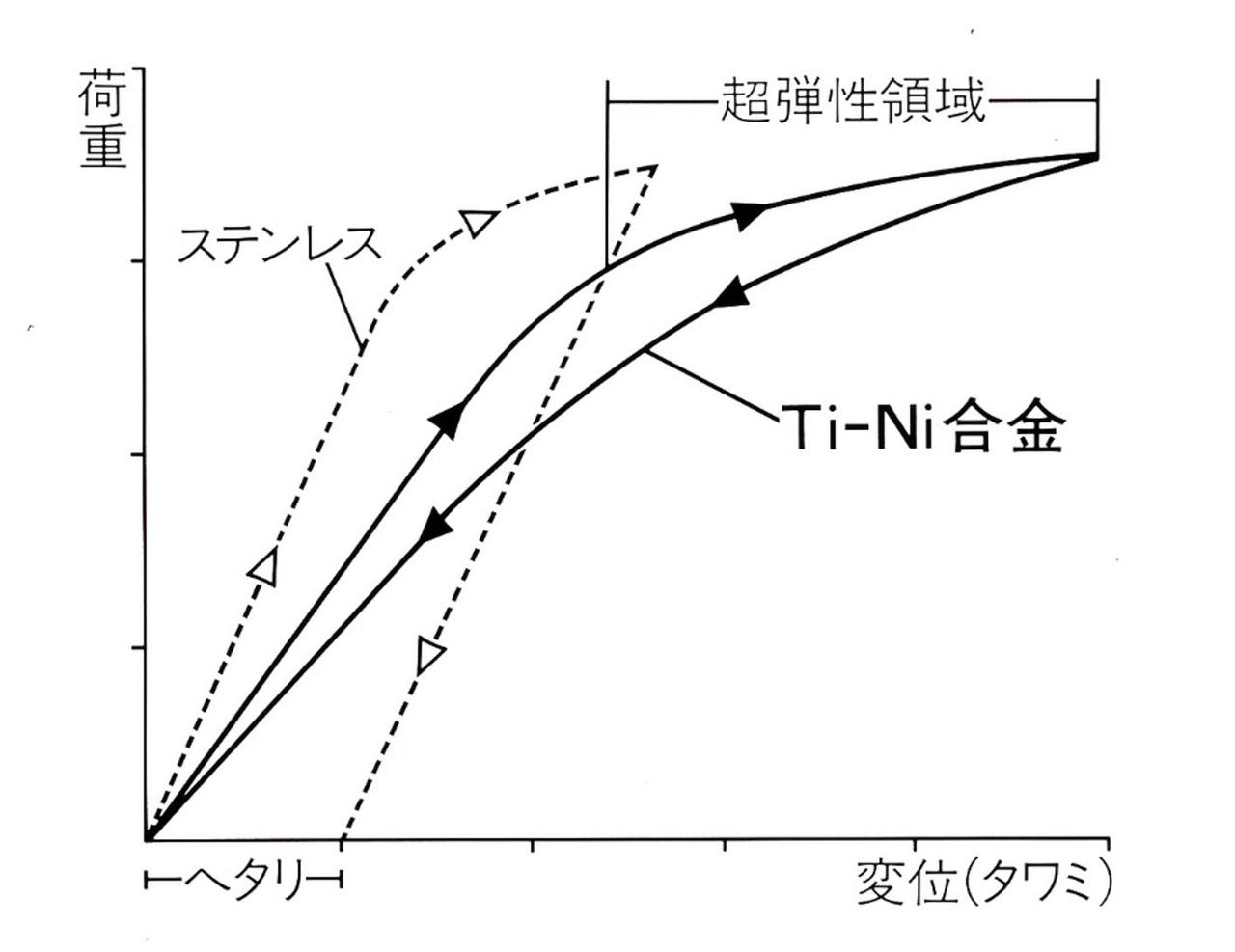
形状記憶合金の応力−歪み特性(ステンレスとの比較)
左右のハウジングを支えるハンガーとヘッドバンドの両端を支える構造部品にはマグネシウムを採用しました。マグネシウムは、比重が1.74で、構造用金属としてはもっとも軽く、プラスチック並の軽さを実現でき、しかもしっかりとした強さで全体を支えます。さらには、振動減衰性に優れ内部損失が大きいため、共振を少なくすることができました。マグネシウムのダイキャスト製法による軽量で高剛性を実現する機構は、R10以降も多くのポータブルオーディオ機器で幅広く採用されていくことになります。
※後編に続く