ステレオサウンド編集部がアキュフェーズ本社を訪問
アキュフェーズは1972年に創業し、半世紀にわたりオーディオ機器を作り続けている老舗のオーディオメーカーです。音質の追求だけではなく、「壊れにくいものを作る」「修理しやすいものを作る」「ライフタイム・アフターサービス(※)」など、創業当初からの基本方針を受け継ぎ、現在に至るまでこだわりのものづくりを貫いています。
ステレオサウンド社の試聴室でも長年、アキュフェーズ製品をリファレンス機器として使わせていただいています。
この度、同社のご厚意により、ステレオサウンド編集部は神奈川県横浜市にある本社の見学に招待していただきました。本稿では、編集部の(つ)と(い)が、訪問時に印象に残った社内の様子と、製造工程から見えた「こだわりのものづくり」の模様をお伝えします。
(※)ライフタイム・アフターサービスとは
お客様がお使いいただく間は、修理・サポートを続けるというアフターサービスに対するポリシー。
「量より質」を体現する生産ライン
アキュフェーズ本社は2つの社屋に分かれています。正面入口の左手に見える第一社屋は、創業間もない1973年に竣工し、2階に設計・開発部門、3階に製造部門が入っています。正面右手には、2020年に新たに建てられた第二社屋があり、1階から2階相当までが吹き抜けの倉庫、3階が品質保証・アフターサービス部門、そして4階に第二試聴室があります。
今回は、製造部門(第一社屋)と品質保証・アフターサービス部門(第二社屋)を主に見学させていただきました。まずは、製造部門からご紹介したいと思います。
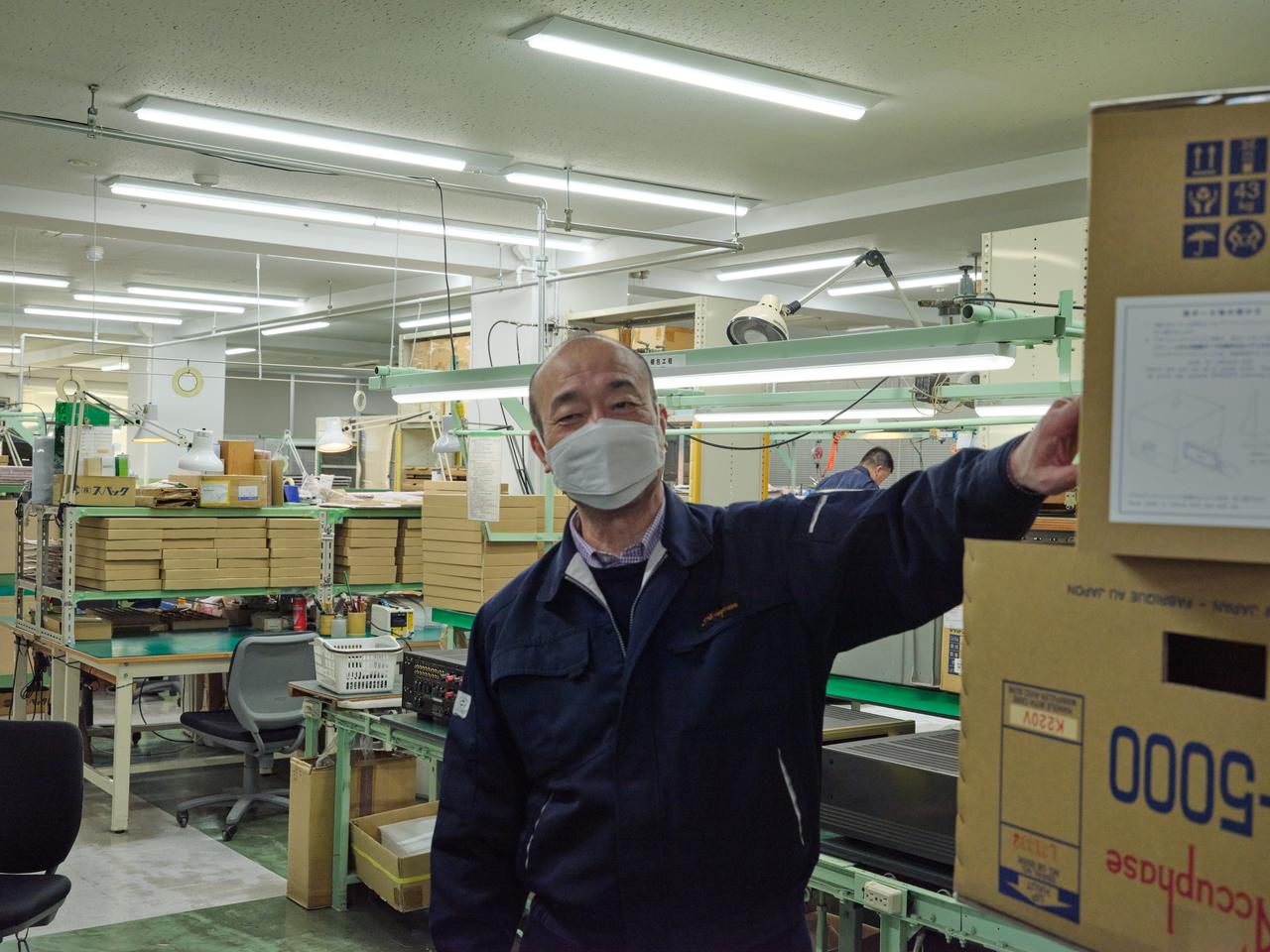
鈴木雅臣代表取締役社長に案内していただきました
製造部門では、およそ10の工程を経て一つの製品が完成します。一貫して妥協しないものづくりを通じて高品質を追求するアキュフェーズでは、どの工程にも熟練の職人がいて、ひとつひとつ手作業で組み上げていきます。加えて、品質チェックにも万全を期しており、複数の検査工程を経てから世に送り出されます。
さらに、すべての製品で高い品質を保つために少量生産方式を採用していて、生産台数は年間5,000台、一日あたり20台ほどに限られるとのことです。
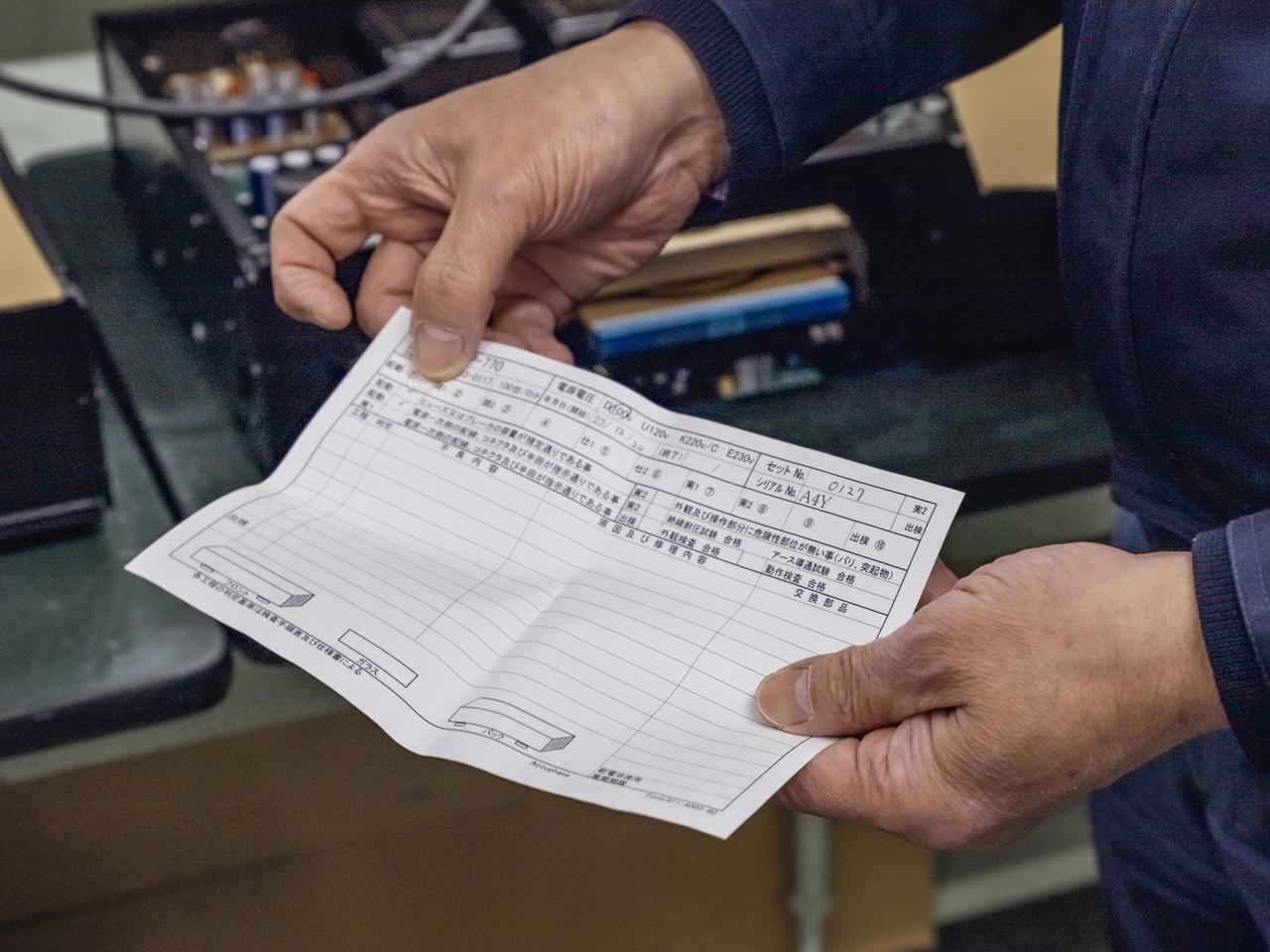
一台一台に付けられる「製品履歴カード」に、製造過程が記録されていきます
すべての製品(個体)には、検査項目をクリアーしたかどうか、汚れ・ホコリを取り除いた箇所の有無など、各工程の経過を記録した「製品履歴カード」が付けられていることも、同社の生産ラインの特徴のひとつです。驚くべきことに、創業時からすべての製品履歴カードが保管しており、故障発生時や修理対応時に活用されているそうです。
それでは、各工程について順を追って紹介したいと思います。
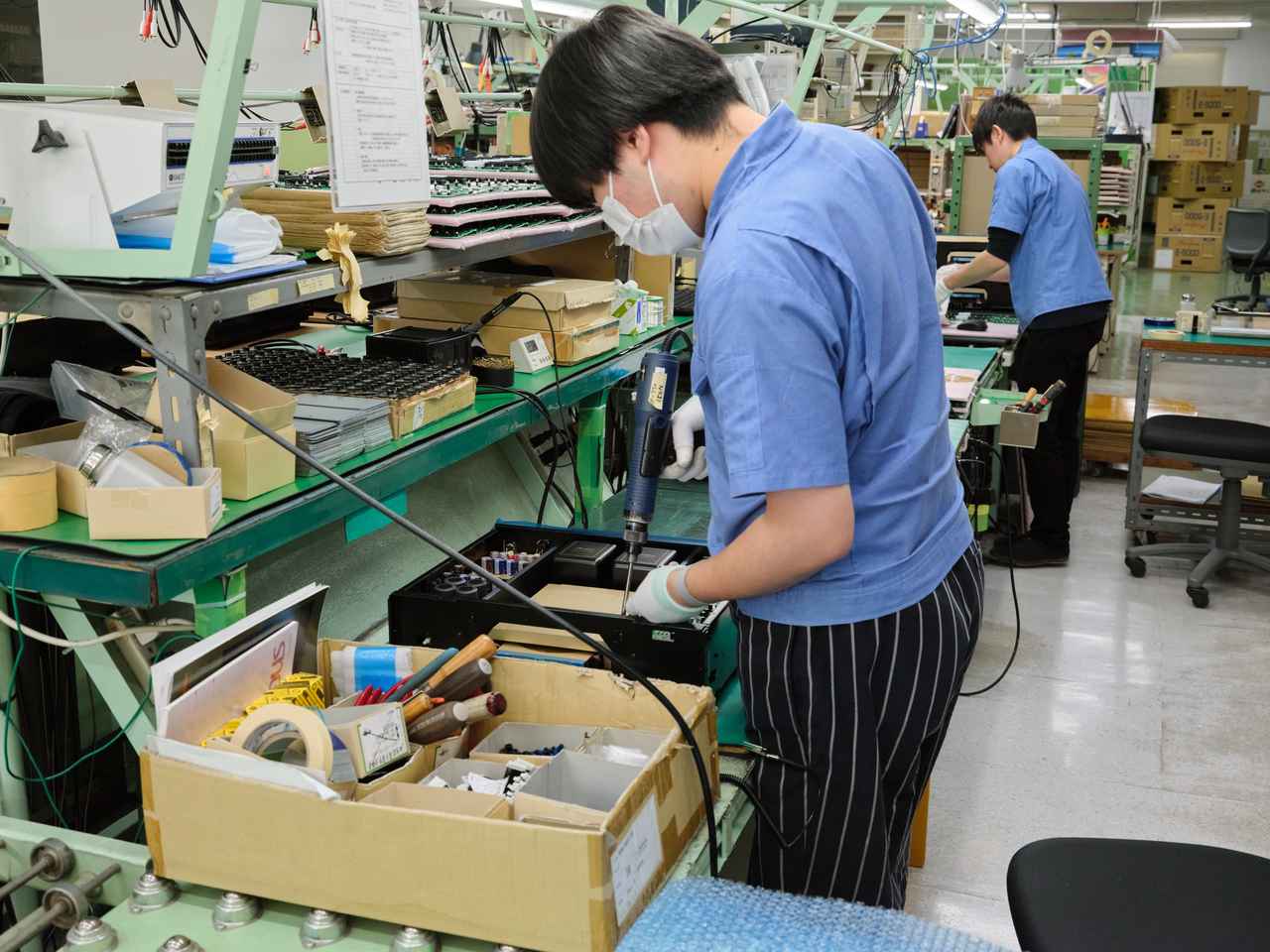
①本体組み立て・配線
シャーシに部品・回路アッセンブリーを組み付けます。
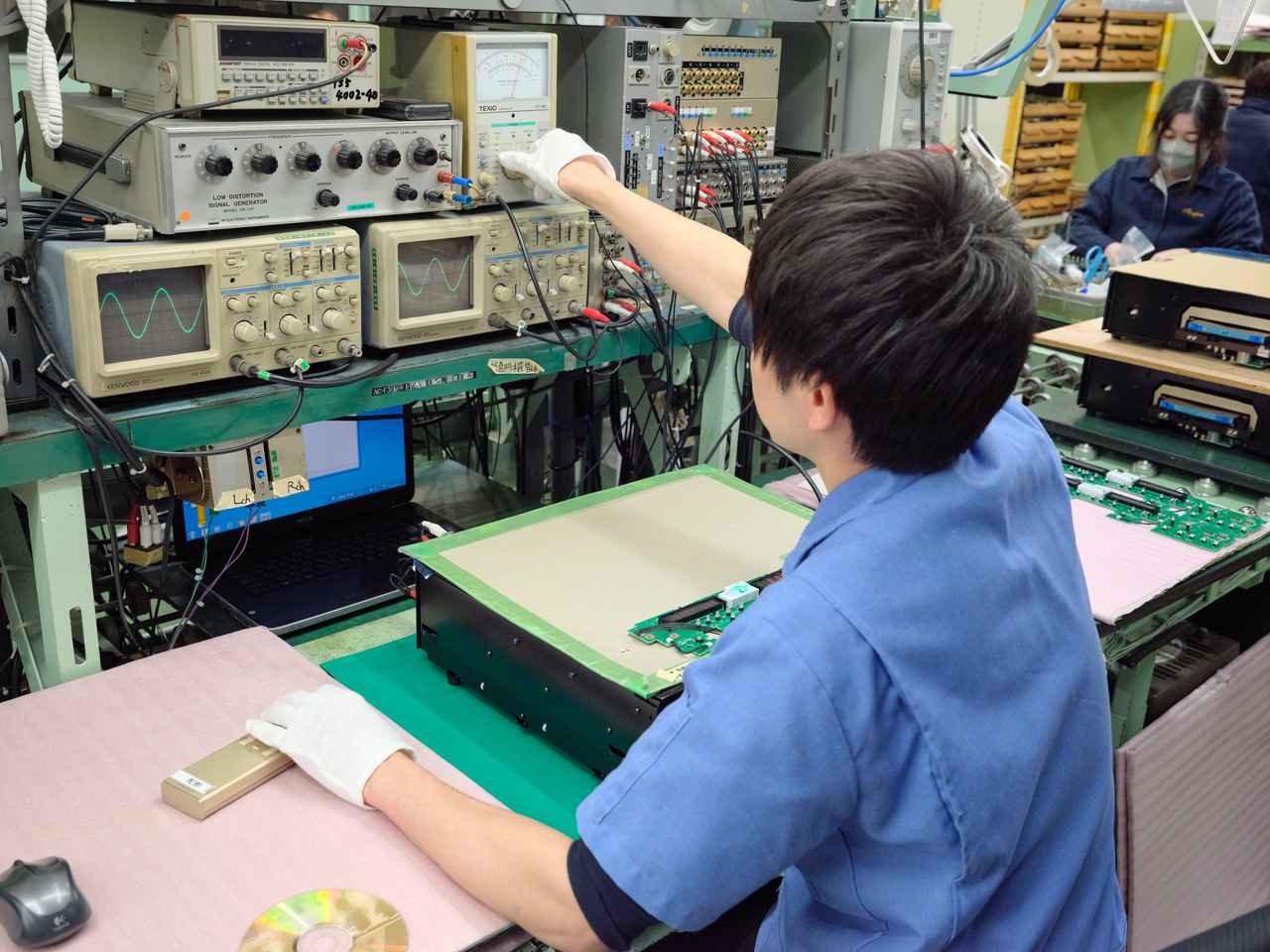
②配線・動作検査
組み付けた部品の配線や基本動作のチェックを行ないます。
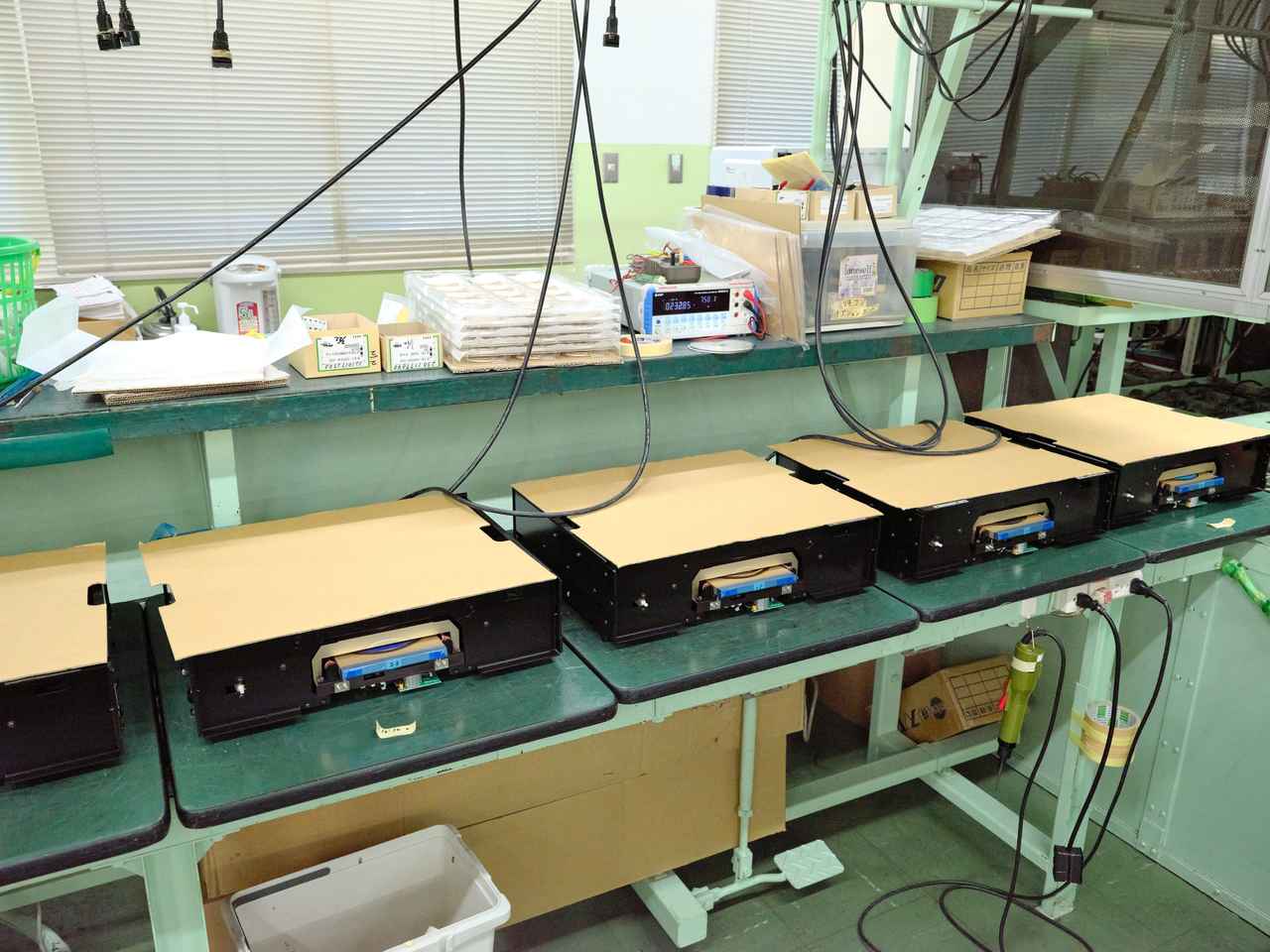
③エージング
電気的な動作や、絶縁の不具合を確かめるために、24時間通電する連続運転試験を行ないます。
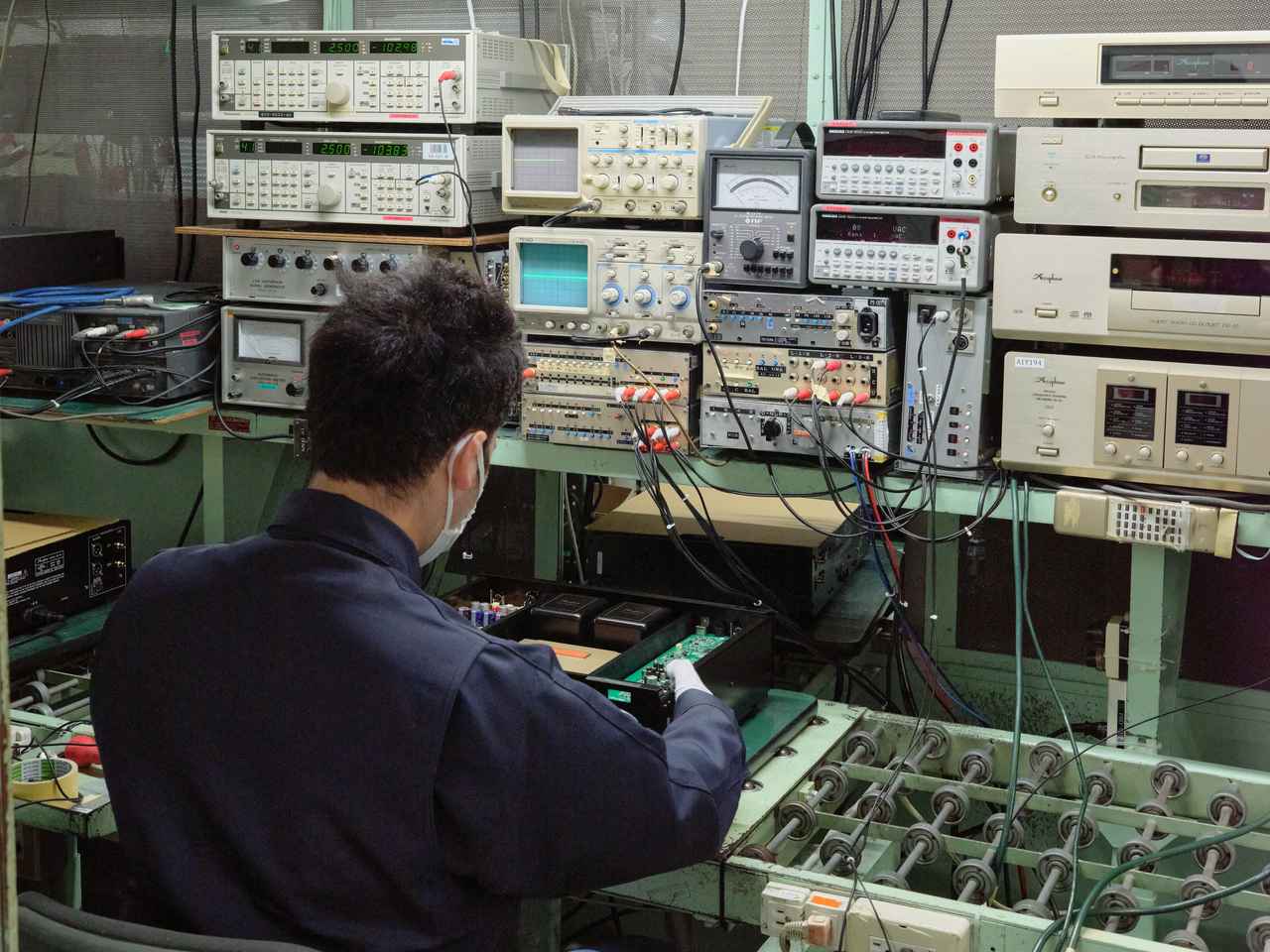
④全項目の測定・調整・検査
すべての項目の性能測定を行ない、さらにパワーアンプとプリメインアンプの内部配線は、オシロスコープで確認しながら、磁力線による歪みが最小になる位置に調整されます。検査基準を満たすだけにとどまらず、製品の性能が最大限発揮できるポイントまで追い込んでいます。
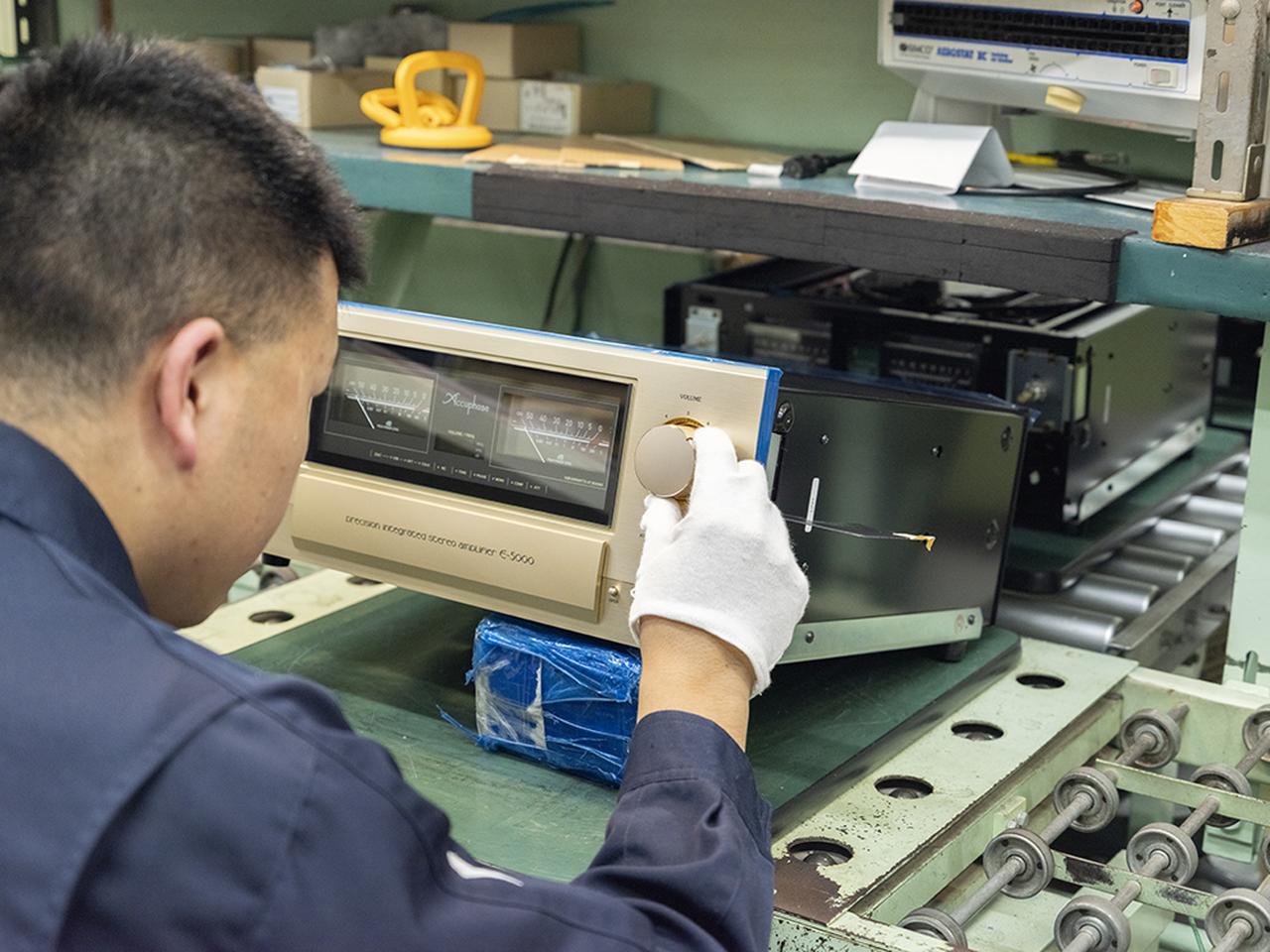
⑤仕上げ(外装部品の取り付け)
キズが付くことを避けるために、パネルなどの外装部品は最後に取り付けられます。アキュフェーズはツマミやスイッチの精度に加えて、操作感にも強いこだわりを持っています。ツマミを回転させたときに、周囲の間隔が一定になるようにするセンター出しにも余念がありません。
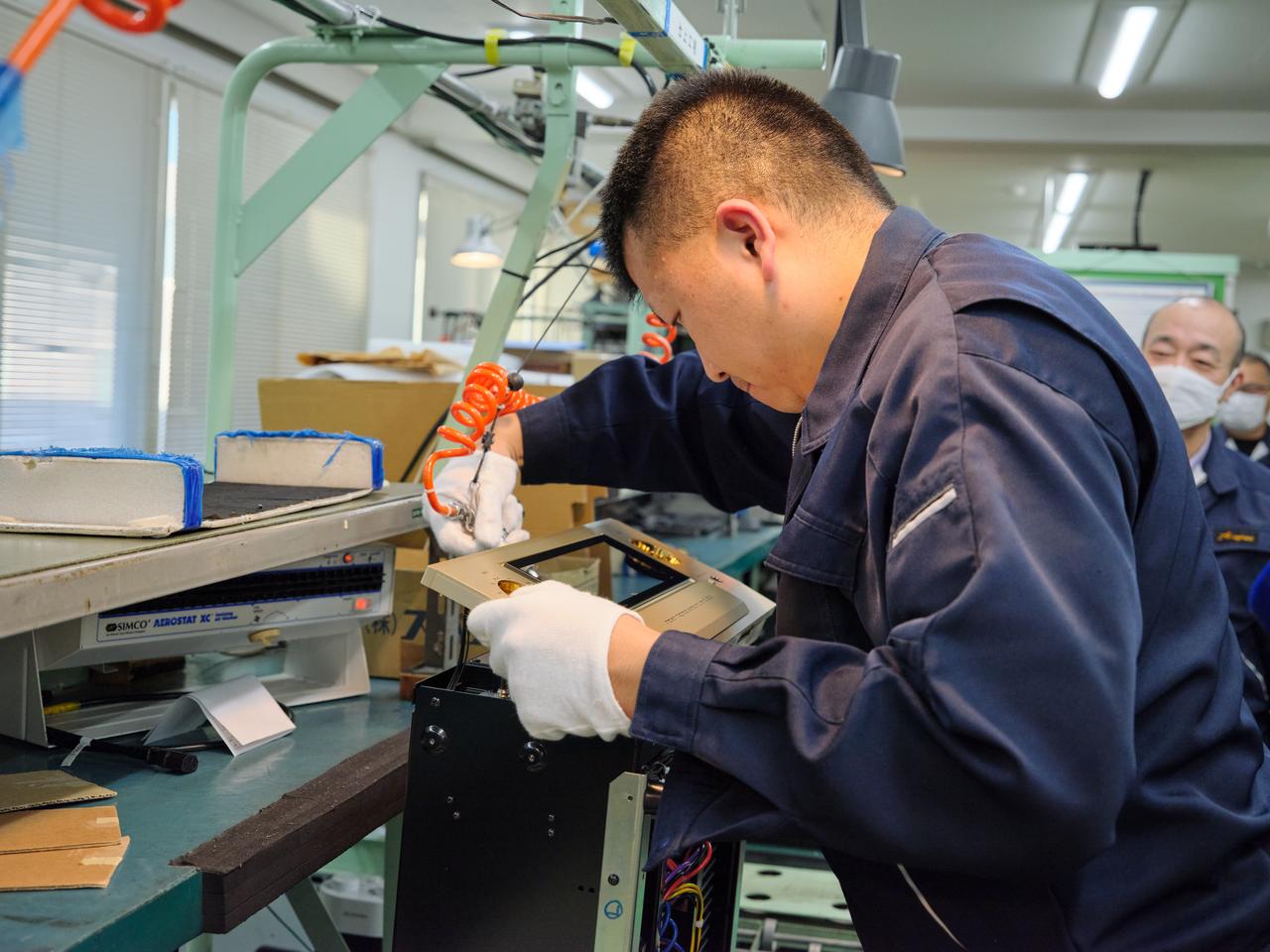
ガラスパネルをはじめとする位置出しが必要な箇所は、あらかじめ微調整できるように設計されています。部品の取り付け後に、内部にホコリが見つかった場合は、パネルを一度取り外して、ブロアーで丁寧に取り除くという徹底ぶりです。
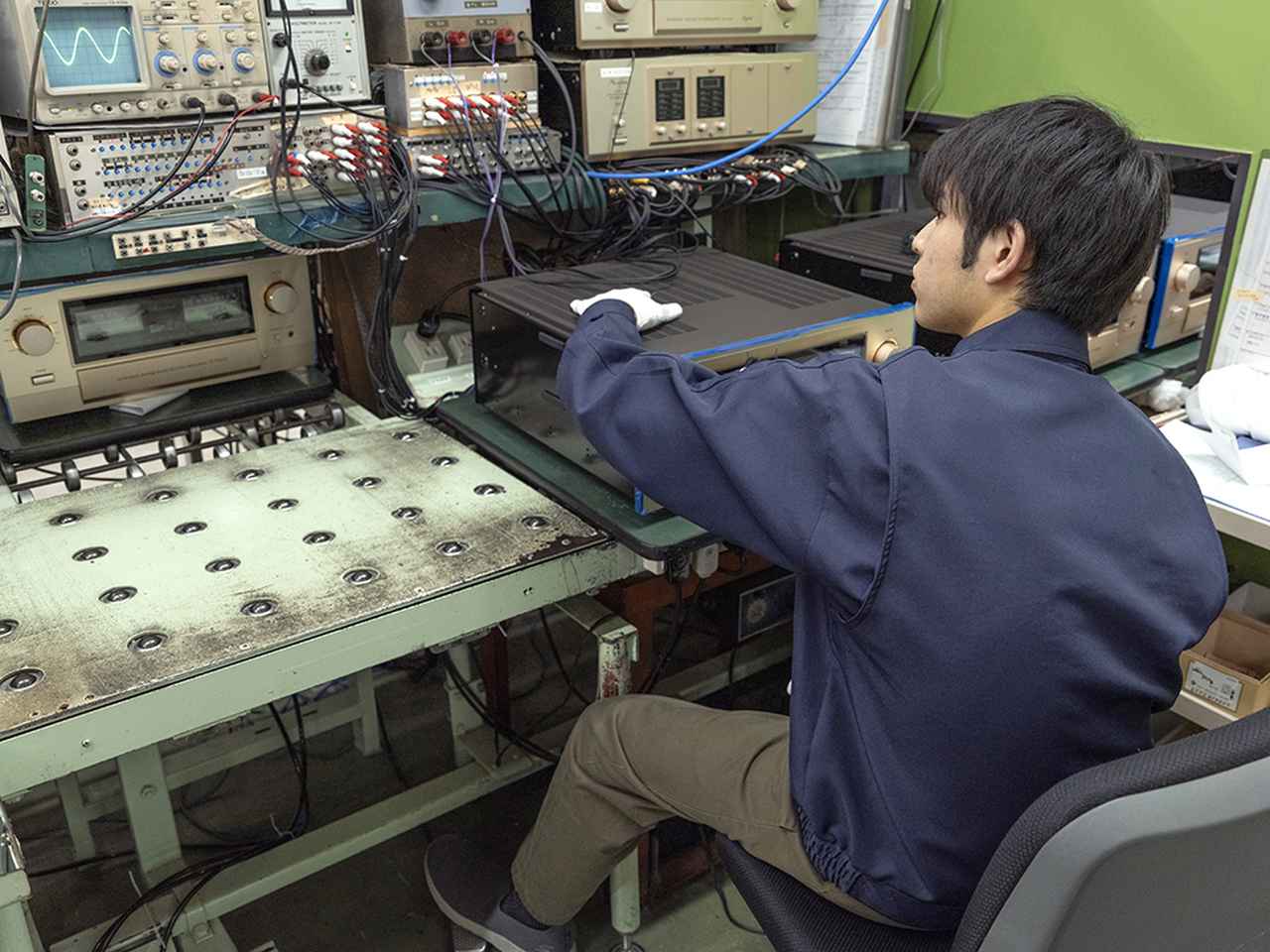
⑥振動試験
組み立てが完了した製品に加振機や手で振動を加えて、ハンダ付けの不良やコネクターの接触不良、混入した異物がないかなどを調べます。
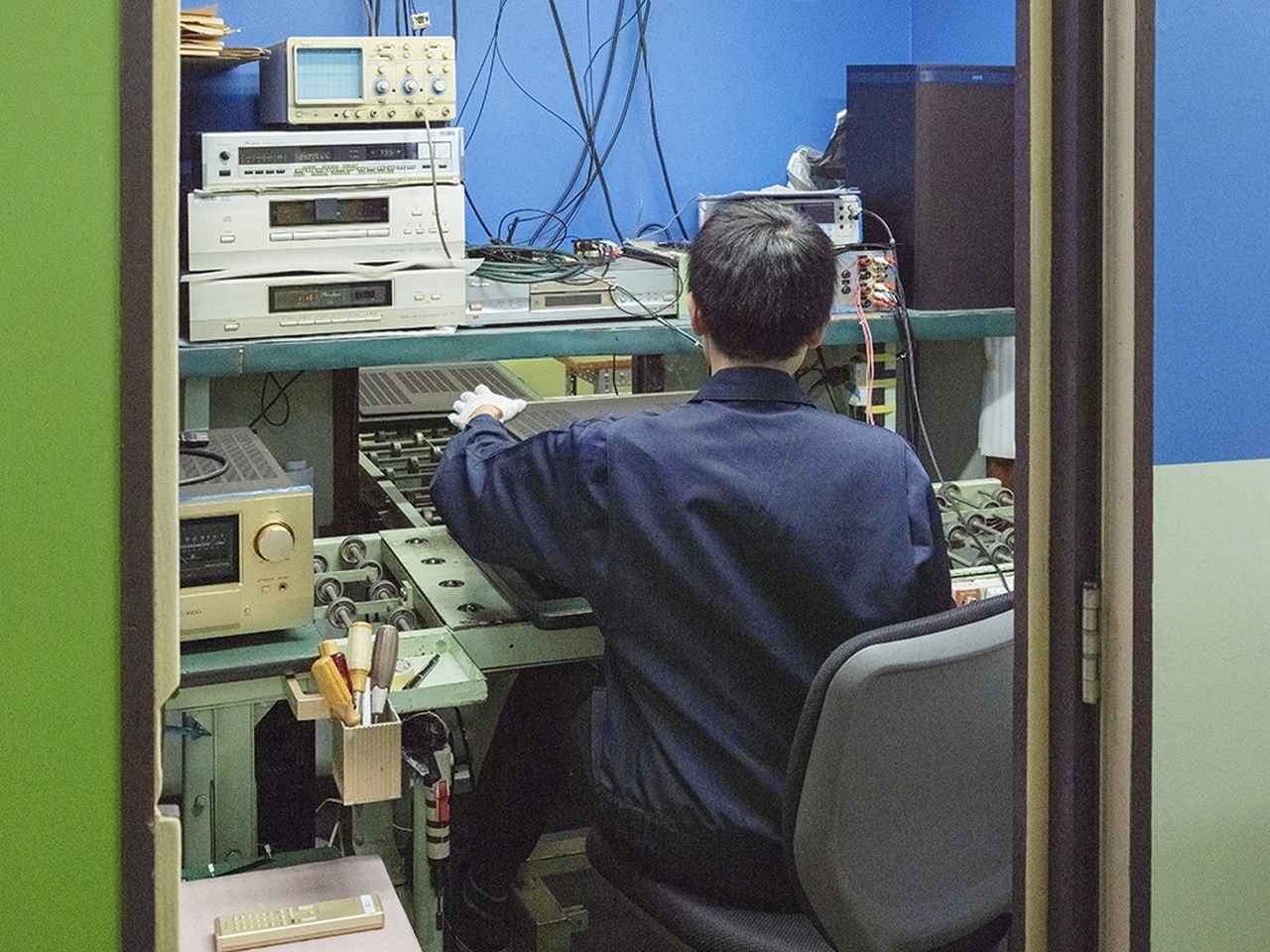
⑦実働検査~⑧安全試験
実働検査では、実際に音を出して、ツマミを操作したときの雑音の有無や、操作感、フロントパネルの明るさ、スイッチの動作音をチェックします。最後に電源部の絶縁試験とアースの導通試験を経て、製造部門の工程は終了です。
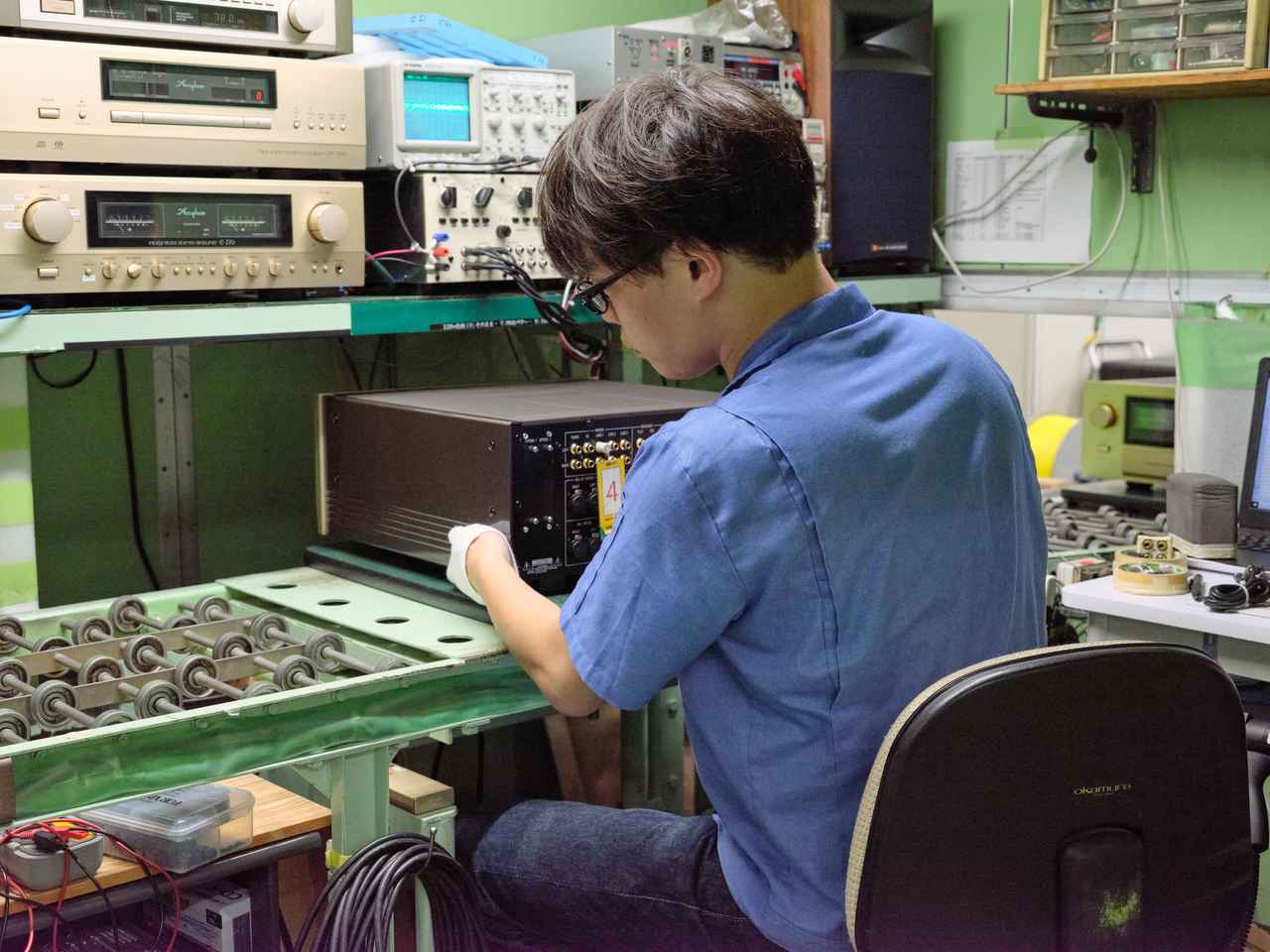
⑨出荷検査
梱包前の最終工程が、出荷検査です。製造ライン内の小部屋で、品質保証部が独自の基準に沿ってすべての製品の検査を行ないます。アキュフェーズでは、一般的な抜き取り検査ではなく、全数検査を実施することで、高い品質を維持しています。
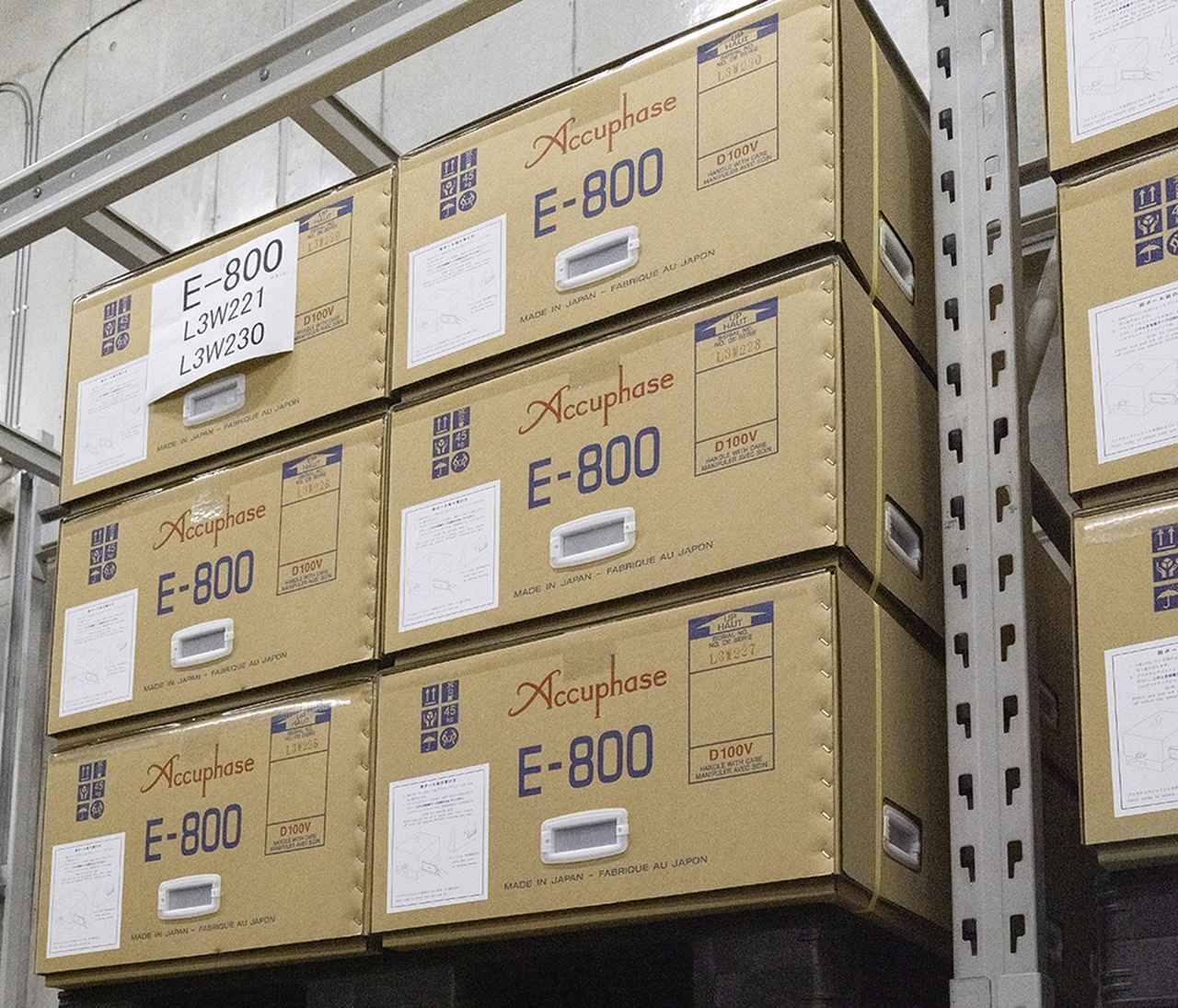
⑩梱包
①~⑨の工程を経て、梱包された製品は第二社屋の倉庫に運ばれます。
ちなみに、CD/SACDプレーヤーのドライブメカ(メカエンジン)は、モーターとピックアップなどで構成されるトラバース部分以外は基本的に自社製です。そのため、メカエンジンは生産ラインとは別工程で組み立てられ、まずは当たり出しのために単体で100回程度のトレイ開閉テストが行なわれます。この開閉テストをクリアーしてはじめて、シャーシに組み込まれ、さらに他の製品と同様の試験を受けることで、品質にこだわったCD/SACDプレーヤーが作られています。
このように、アキュフェーズの生産ラインでは、検査だけでも6つの工程があり、さらには製造部門と品質保証部のダブルチェックを経て、ようやく一台の製品が世に送り出されます。まさしく、「量より質」を体現している生産ラインだと言えるのではないでしょうか。
製品の修理・メインテナンスの最前線、アフターサービス部門
「ライフタイム・アフターサービス」が企業ポリシーのひとつであるアキュフェーズでは、2023年からCDプレーヤーを含むほぼすべての製品で5年間の無償保証期間を設けています。さらに、過去に販売したすべての機種の修理を可能な限り受け付けていることも、自社でものづくりを行なうアキュフェーズならではと言え、揺るぎない信頼性の土台になっています。
そうした手厚いアフターサービスを一手に担うのが、第二社屋にあるアフターサービス部門です。訪問時には30年以上前に発売されたプリメインアンプ「E305」(1987年発売)のメインテナンスが行なわれていました。
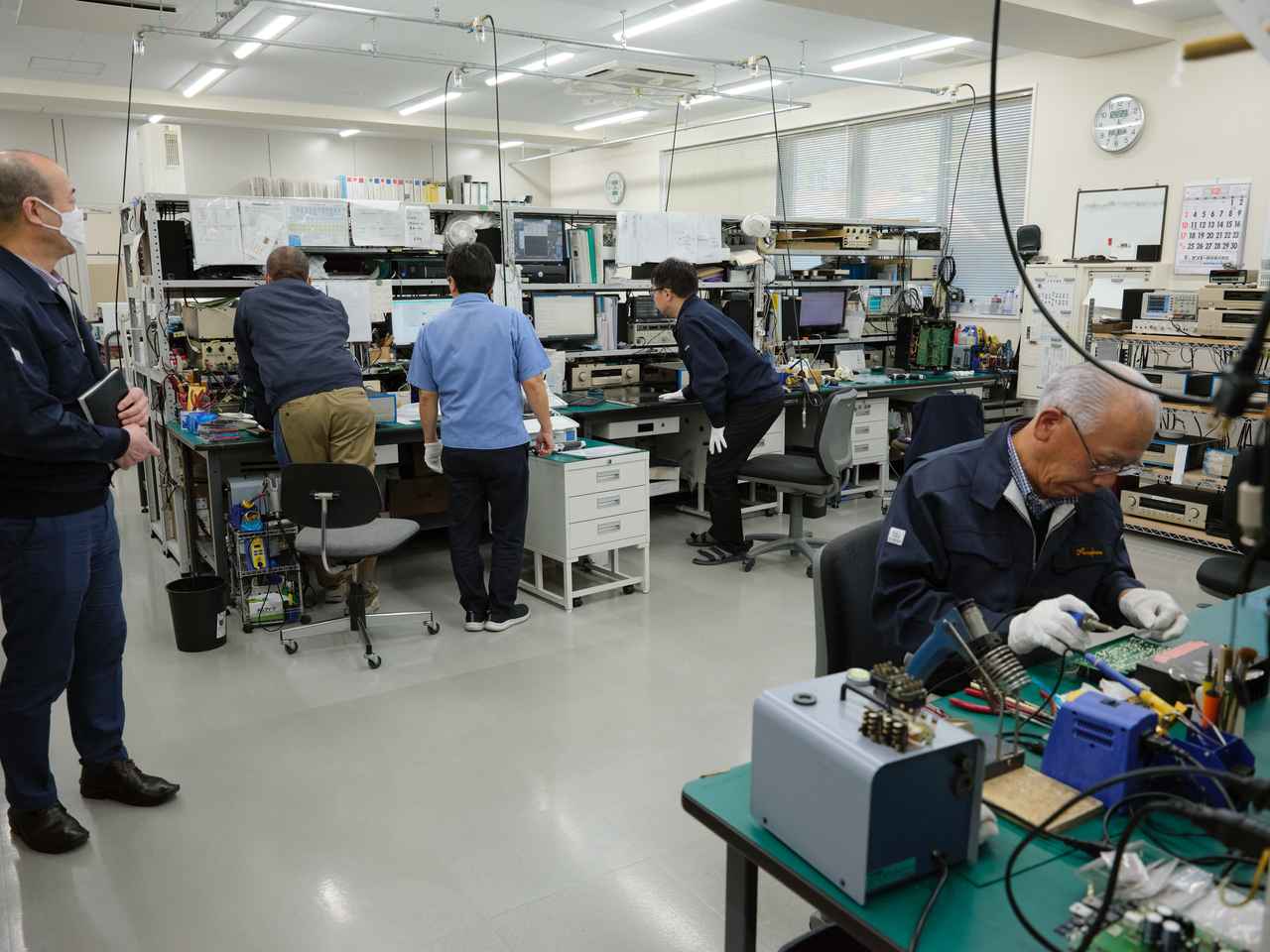
第二社屋にあるアフターサービス部門では、年間2,000台もの修理を行なっています。
とは言うものの、250機種を超える歴代製品の部品をすべて保持することは難しく、製造中止になって入手が難しくなっている部品も少なくありません。当時の部品で修理できないものは、近い性能を持つ部品を用いて、形状が合うようにコネクターを作って修理することもあるそうです。
さらに、古いリレーは修理後に長く使えるように、劣化を防ぐためのパッキングを施したり、寿命を考慮してオリジナルと異なる素材の絶縁シートに交換したりと、ひと工夫施すことで、製品が持つ性能をより長く維持できるようにしているそうです。お客様からは、「修理から戻ってきたら音が良くなった!」という喜びの声も届いていると言います。
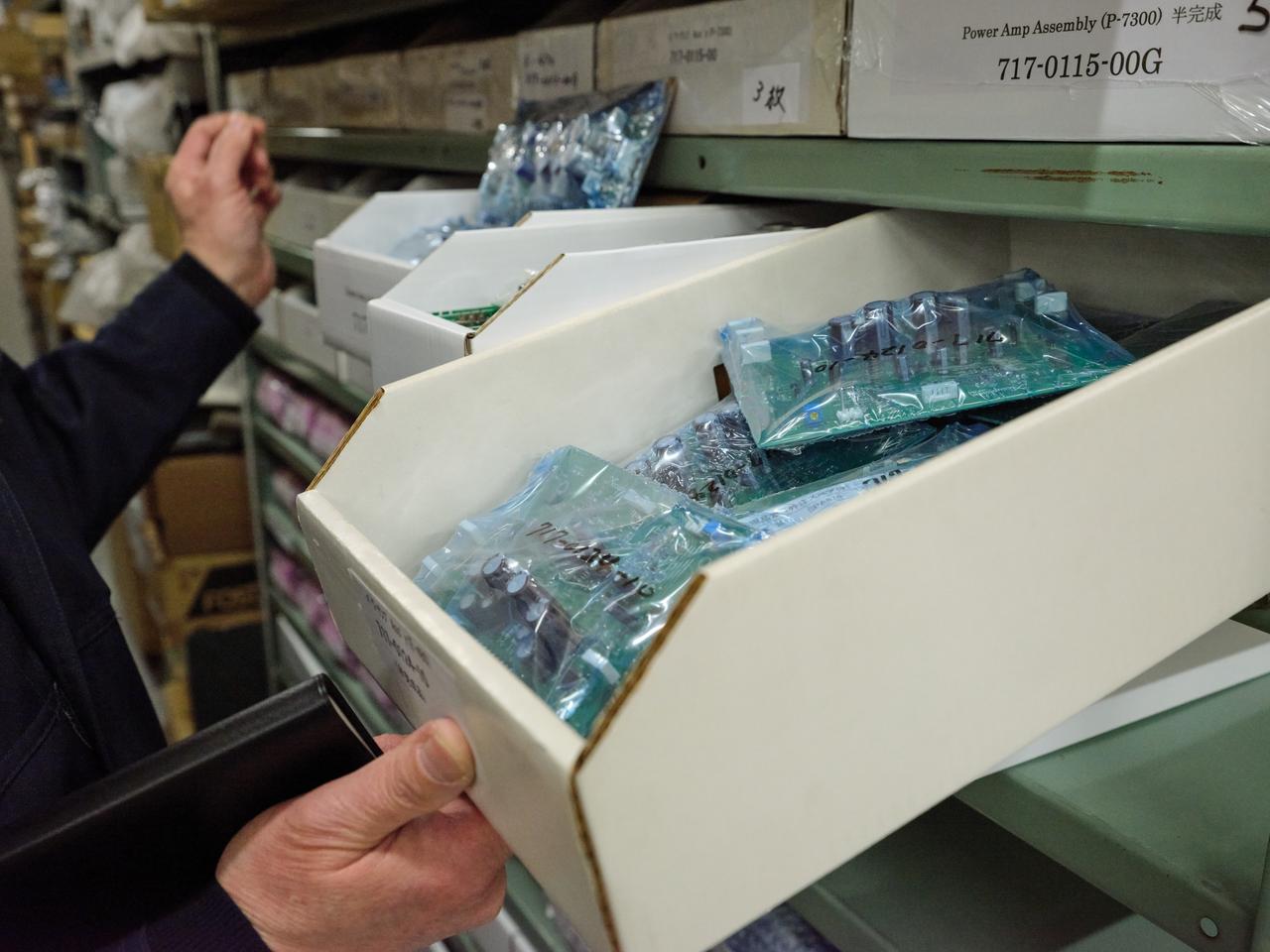
保管している修理用部品は、製品・パーツごとに細かく整理されています。中にはフロントパネルまで保管されている製品もありました。
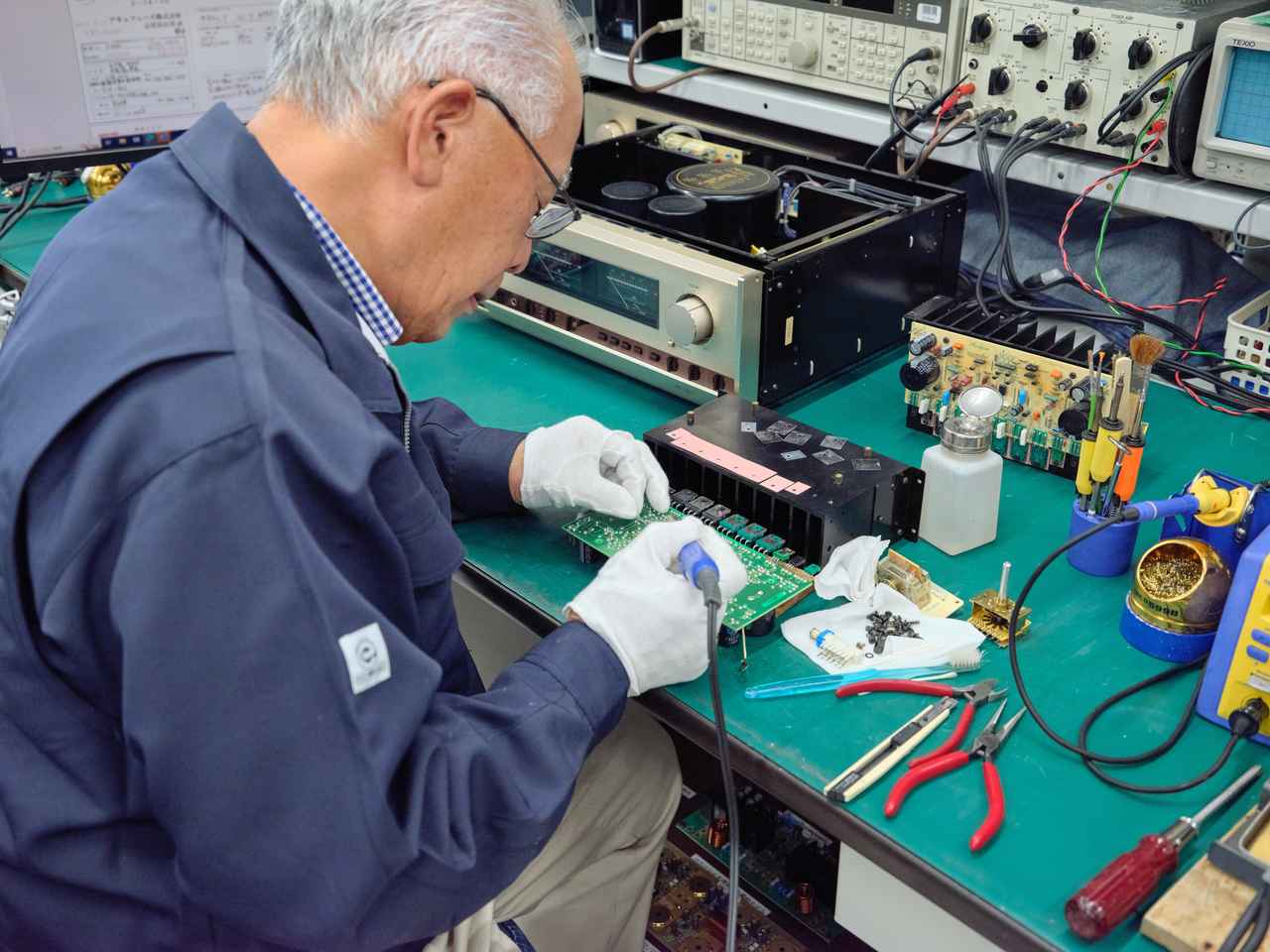
オーディオ店での講演でも知られる、アフターサービス部門のベテラン・渋谷清さん。
出荷を待つ製品たちは倉庫で眠る
2020年に新設された第二社屋の1階は、厳正な検査をクリアーし、出荷を待つ製品が保管されている倉庫です。2階まで吹き抜けの構造になっており、最大4,000台の製品が保管できます。
日本だけではなく、海外での人気も高いアキュフェーズ製品。倉庫には、ヨーロッパ向け、アジア向けなど、出荷地域ごとに箱が分けられていて、その人気の高さがうかがえます。
箱の印字を見ると、国ごとに規格や電圧が違っています。なんとアキュフェーズでは、出荷地域を問わず、各国の安全基準のなかで最も厳しい規格に合せて、すべての製品設計を行なっているのです。そのため、電源電圧を変更している点以外は、日本向けと海外向け製品の違いはないと言います。ものづくりへのこだわりようは、倉庫からも垣間見えました。
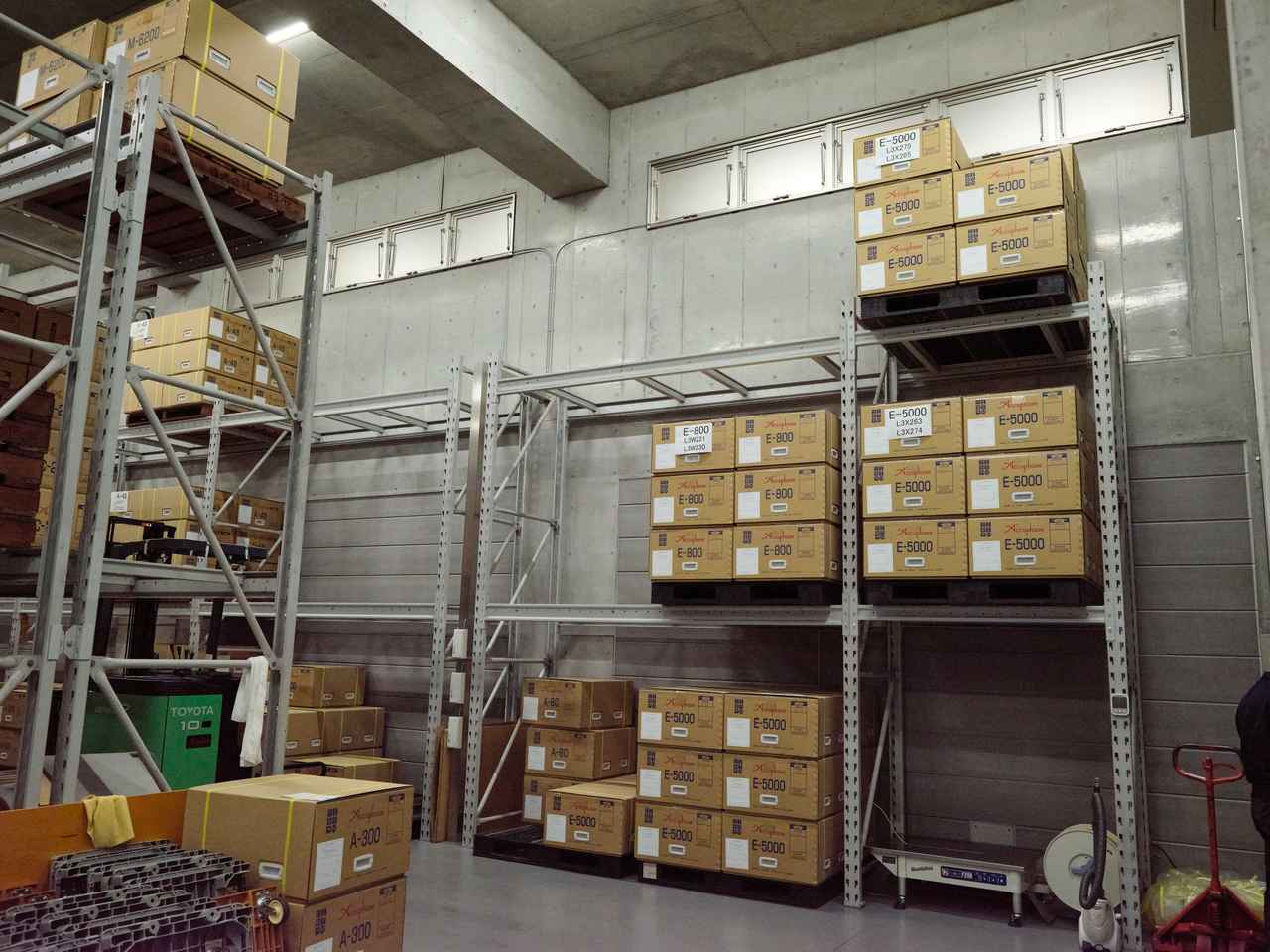
第二社屋1階の倉庫には、最大4,000台の製品を格納できるそうです。
ユーザー目線で音づくりをするための第二試聴室
第二社屋の最上階には、床面積は26帖、天井高は最大3.5mを誇る第二試聴室があります。製品開発で音を詰めていく第一試聴室と、よりユーザー目線での試聴が行なえる第二試聴室の両方を活用することで、新製品の音が固められていきます。
この第二試聴室にはリファレンススピーカーとして、ファイン・オーディオ「F1-12」とB&W「800D3」の2機種が導入されています。見学の最後に、ケルテスが指揮した『ドヴォルザーク:新世界より』(SACD)、アデル『30』(LP)、福山雅治『魂リク』(LP)を2種類のスピーカーを切り替えながら聴かせていただきました。
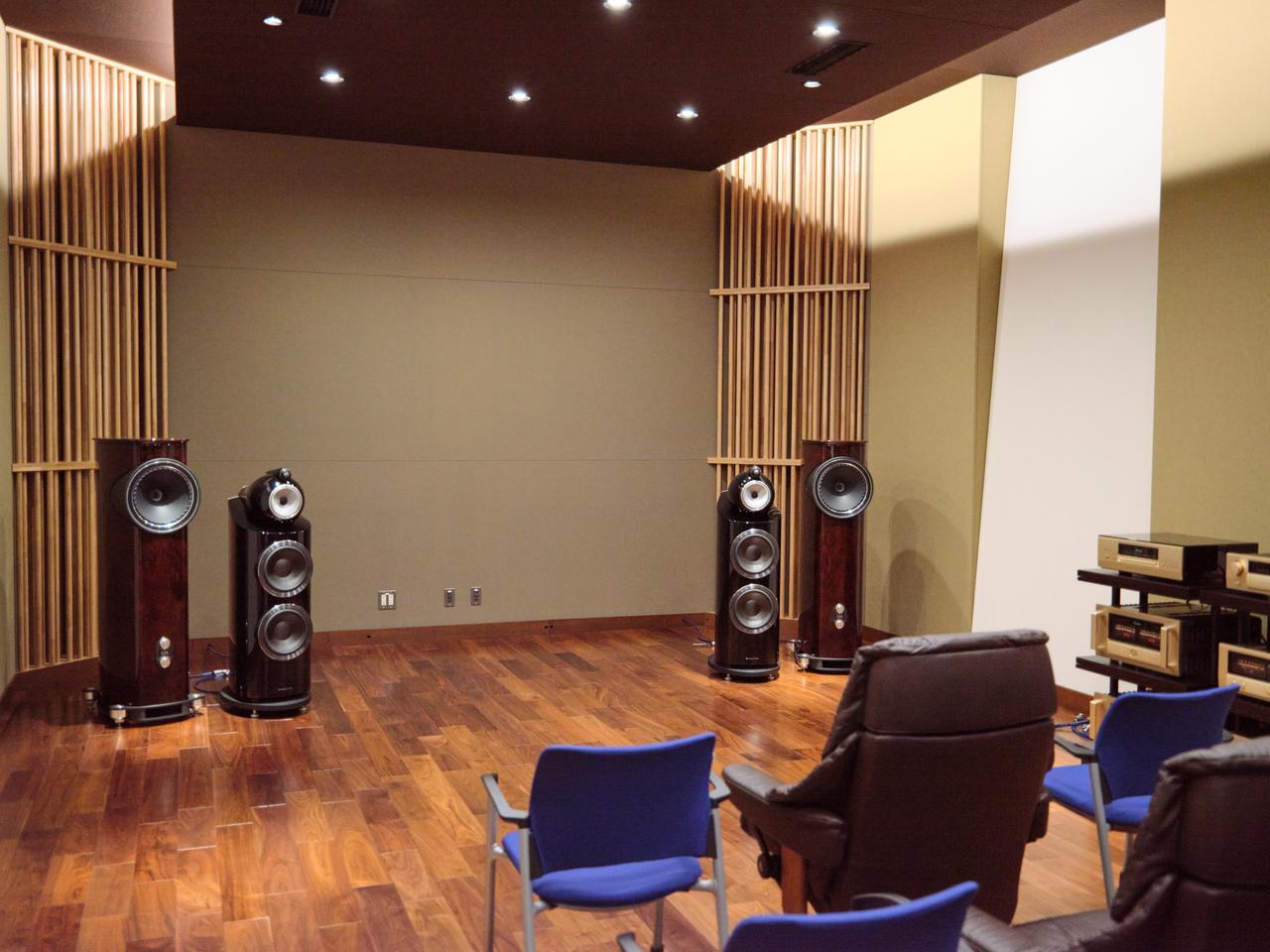
26帖の広さを誇る第二試聴室で、実際に音を聴かせていただきました。
アキュフェーズ本社訪問を終えて
半日にわたって、アキュフェーズ本社を案内していただき、長い歴史の中で創られてきた同社の「こだわりのものづくり」の現場を体感しました。また、手作業で行なわれる組み立てや、厳重な品質管理、長期信頼性・安全性を担保するメインテナンスの現場などを間近に見ることで、永く愛される理由を感じ取ることができました。
職人の方々の手を経て完成した製品を一人でも多くのオーディオファイルに体感していただきたいと思うと同時に、リファレンス機器として同社製品を身近に感じている我々ステレオサウンド編集部も、さらに気を引き締めて使わなければ、と気持ちを新たにした次第です。
オーディオ評論家の山之内 正先生がアキュフェーズ本社を訪問した
動画もぜひご覧ください!
Accuphaseの新しい試聴室を大公開。いい音はここから生れる! [Accuphase facility Tour Vol.1]
www.youtube.comAccuphaseの生産工場へ潜入。そこにあるのは「信頼」の2文字だった [Accuphase facility Tour Vol.2]
www.youtube.com