飯田ピアノは、KuraDaブランドとして6年ぶりとなる新型ヘッドホン「KD-Q1」を発表した。市場想定価格¥220,000前後(税込)で、8月5日(月)の発売を予定している。これに先立ち、本日KD-Q1の製品発表会を開催した。
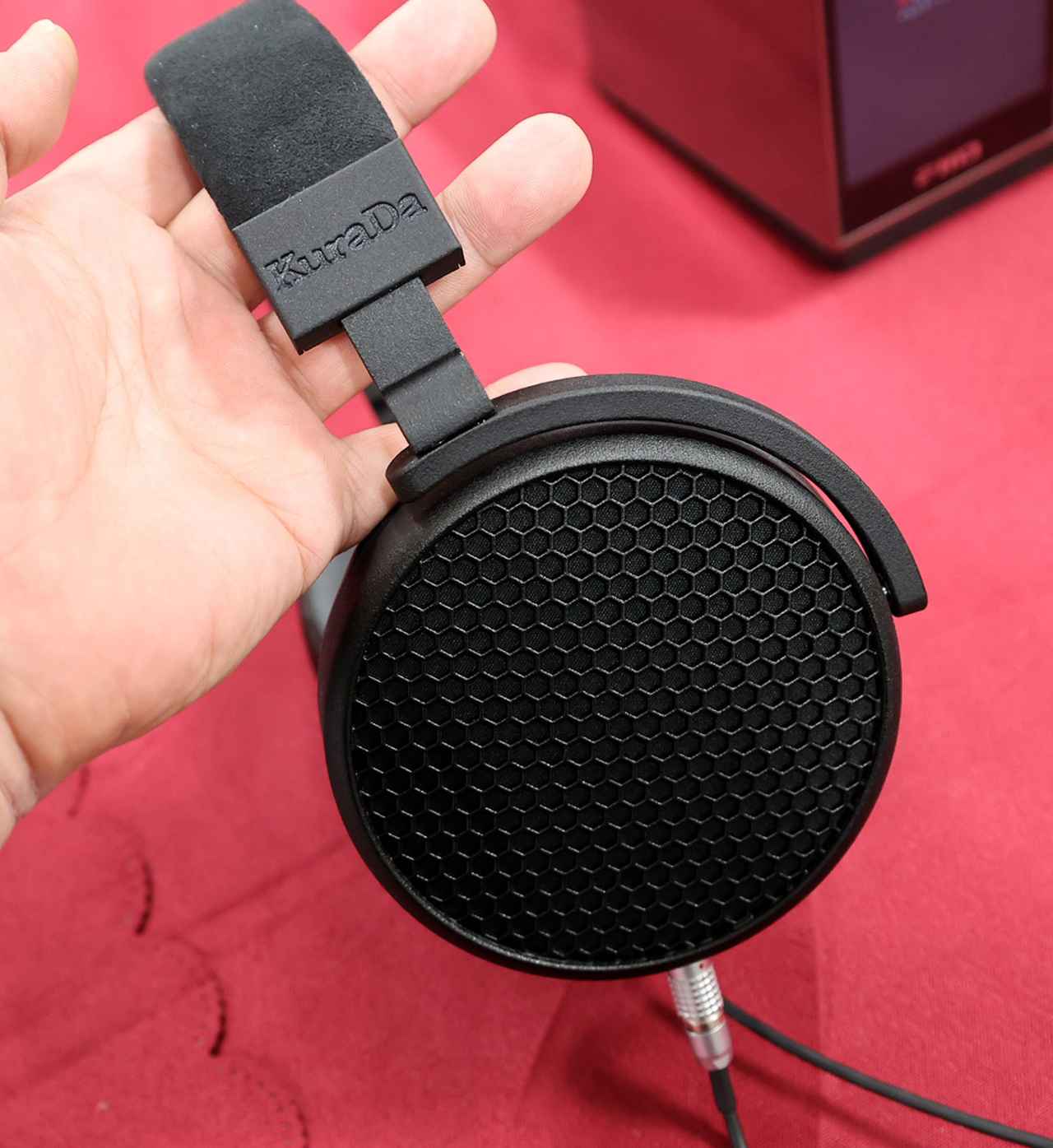
新製品ヘッドホン「KD-Q1」。表面のハニカム構造も3Dプリンターでひとつのパーツとして成形されている。表面には傷にも強い塗装を施し、耐久性を向上させた
KD-Q1は3Dプリンター技術を駆使したオーバーイヤー型ヘッドホンで、軽量で高い強度を備えた「PA12GB」素材を採用し、音質・耐久性・快適性を高い次元で実現したという。複雑な内部構造が可能となり、さらに振動板の動きを最適化したことで音楽のディテイル再現も向上しているそうだ。
発表会は、神奈川県大和市にあるSOLIZE株式会社の工場で行われた。ここは実際にKD-Q1のパーツを、3Dプリンターを使って製造している拠点となる。
KuraDa代表の飯田良平さん
まずKuraDa代表の飯田良平さんが登壇し、KD-Q1の技術詳細について紹介してくれた。そもそもKuraDaは2012年に誕生したブランドで、これまで2013年の「KD-FP10」、2014年の「KD-C10」、2015年の「KD-P1」といった製品を生産・販売してきている。それらのパーツにはすべて日本製を使うなど、国産にこだわった物作りも行われてきたそうだ。
ブランドの理念として、「常に革新的であれ」「常に最良であれ」「常に謙虚であれ」という3つを掲げ、KD-Q1でもそれらに則した製品開発を行ってきている。
まずKD-Q1で革新的なのが、上記した3Dプリンターによる製造・生産に取り組んだことだ。これまでのKuraDaヘッドホンは金属の切削加工で作られることが多かったが、その場合、高精度な加工と美しい表面仕上げが可能な反面、高コストで複雑な形状の場合は量産が難しいという問題もあった。これに対し3Dプリンターならデザインの自由度が高く、低コストで複雑な形状のパーツでも製造できるというメリットがある。今回はその点に着目したとのことだ。
そこで使われているのが、HP Jet Fusion方式の3Dプリンターだ。これは細かい粉末素材に液体を加えて加熱することで任意の形状のパーツを製造できるもので、同様の3Dプリンターに比べて高速での部品生産が可能で、より高精度なパーツを作れるのが特徴という。
材料となる粉末素材には「PA12」という直径50ミクロンほどの材料に40%程度ガラスビーズを混合している(=PA12GB)。これを使うことで曲げに対する耐性、引張強度が高い部品を製造できるという。同時に軽量で内部損失も高いなど、オーディオ用として理想的な特性も備えている。なお残った粉末素材の70%は再利用可能なので、エコにも貢献できるとのことだ。
製品発表会で、実際に3DプリンターでKD-Q1のパーツをプリントアウトしている様子を見せてもらった。幅5m、奥行2mほどの巨大な3Dプリンターの中央部に粉末材料を格納したユニットが収まっている。この粉末をトレイ全面に薄く敷き、その上に部品の平面データ(CADで制作した設計図)に準じた形で液体が塗布される。この状態で上から光を照射すると液体が塗られた部分だけが硬化して、立体物が出来上がる仕組みだ。
SOLIZEの工場に設置されたHP Jet Fusionの3Dプリンター
SOLIZEにあるHP Jet Fusionでは1回のプリントで18台分のKD-Q1のパーツを製造できるそうで(所要時間は18時間ほど)、KuraDaではこれをロット単位として製品づくりを行っていく模様だ。
ちなみにSOLIZEは1990年創業の、3Dプリンターによる物作りを展開している企業で、3Dプリンターに関連したデザイン、ソフトウェア開発、デジタルエンジニア領域から、3Dプリンターによる物作り、3Dプリンターの販売まで手掛けている。現在大和工場には40台ほどの3Dプリンターを所有しているが、これは日本最大級だという(このうちHP Jet Fusionは5台)。
SOLIZEのデジタルマニュファクチャリングサービス事業部 AMサービスビューロー部 部署長の太田 亨さんは、3Dプリンター技術を使えば、継続的な金型保管が不要で、メインテナンスコストの削減ができ、さらに製品開発時にもリードタイムも短縮できるといったメリットがありますと3Dプリンターの魅力を紹介してくれた。
HP Jet Fusionに格納するユニット。写真右側の赤い矢印部分が粉末材料の「PA12GB」
なお今回のKD-Q1で3Dプリンター技術を採用する際には、使う素材や部品の品質などを吟味したうえで、どの種類の3Dプリンターが最適かという検証や、部品の形状やプリントアウトの際のレイアウトの最適化(もっとも効率のいい図面設計)などの課題をクリアーしたのだそうだ。
同じくデジタルマニュファクチャリングサービス事業部 マーケティング&セールス部の北山成志さんは、KD-Q1では意匠性とコストのバランスを重視して設計したと話してくれた。3Dプリンターは薄い膜を重ねてパーツを出力するため、プリント時の傾きによって表面の仕上がりなどが変化する。1回でプリントアウトできるブロックの中にいかに効率よく、しかもパーツの種類に応じて強度などを考えつつパーツを配置していくためは、高い技術が要求されるのは間違いない。
作動中の3Dプリンター。写真で黒く見えるのが液体を塗布した部分で、光を当てるとここが固まる仕組み
ここから再び飯田さんが登壇し、KD-Q1のヘッドホンとしてのスペックも紹介された。KD-Q1は「Ultra-Responsive Diaphragm」ユニットを搭載している。これは53mmのPET素材振動板にOFCボイスコイルを組み合わせたドライバーで、前モデルと基本的には同じ構造を踏襲しつつ、低域再現性にフォーカスして改良を加えているそうだ。
さらにヘッドホンで重要なイヤーパッドは、低反発ウレタンを3次元形状にカットし、人の頭の形に合うように立体縫製したカバーを組み合わせることで、快適性と音質の両方を獲得している。このイヤパッドは音漏れを最小限に抑えて、しかも適度な側圧で保持することで長時間装着しても疲れにくい特性を備えている。
成形工程が終わったら、左の写真のように、粉末素材の中から固まった部分(KD-Q1のパーツ)を手作業で取り出す。その後余分な粉末を取り除き、塗装を施してパーツとして出荷される
さらにゲストとして麻倉怜士さんが登場、KD-Q1の試聴インプレッションを紹介してくれた。麻倉さん曰く、「まず何と言っても軽くて、手触りがいいですね。イヤーパッドの形状もいいし、側圧もさわやかです」と3Dプリンターでの物作りを高く評価している様子だ。
音質については、「情家みえさんの『チーク・トゥ・チーク』では、ピアノとベースのコード進行、立ち上がりと量感がリッチでキレがいいし、音階もよくわかりました。ヴォーカルとピアノの掛け合いがきちんと再現されているし、ピアノソロでの叙情性が感じられるのも素晴らしい」と声や楽器の再現性もお気に入りの様子だった。
「KD-Q1」の軽さ、装着感のよさに驚いたという麻倉さん
発表会ではFIIOやブリキャスティデザインのヘッドホンアンプとの組み合わせでKD-Q1の音を確認することができた。J-POPやアニメソングなどいくつかの音源を視聴させてもらったが、特に女声が綺麗で、細かな情報もクリアーに描き出す。楽器の余韻の再現も自然で、広がりのある音場を再現してくれた。
また麻倉さんのコメントにあった通り、296gと本体がひじょうに軽いし、側圧も優しい塩梅なので、ヘッドホンを付けていることがまったく気にならない。この快適さは自宅での音楽試聴にも大きな魅力になるだろう。
ケーブルの脱着・交換も可能で、別売りのバランス対応ケーブルを組み合わせれば、バランス接続による再生も楽しめるそう